The problem: Inefficient field communication
Masonry is one of the oldest trades in construction. Although happy with their traditional roots, Stonwerk Custom Masonry wanted to modernize their communication. (And not rely on pen and paper reports.)
The solution: Real-time field data
With Raken, Stonwerk gives their foremen an easy-to-use subcontractor app to log field data. Since reports are uploaded to the cloud in real time, the office has better visibility to win more business.
Passing the craft through four generations
Stonwerk Owner Steve Homola’s family grew up in the industry. In fact, Steve started laying brick with his dad in the mid 1970s. It was in 1985 that he ventured off to start his own business—this time, in masonry. What started as a one-employee company grew into a family legacy.
“I think I had one employee for a few years, then two, then five,” Steve said. “Now, my children are old enough to come and work for the company. We've even got one of my grandchildren working for us. So it's four generations of masons."
According to Steve, there’s a big difference between brick and stone. While brick is all about layout, stone has more of a mental state to it. Even with 10 guys on a job, their chats are cut short to focus.
“When you get to stone, usually you don’t start out with any lines. You just have a pile of rock that you have to make look nice on the wall,” Steve said. “When you’re laying stone, you don’t hear much conversation. There’s mental preparation involved, but that’s the craft of stone masonry.”
Modernizing their project documentation
When Reed Homola, Steve’s son and Operations Manager, first started out, Stonwerk was still using “clunky” Excel spreadsheets. That made it hard for field crews to document their progress—leading to crucial details being left out.
“I don’t think there were any photos,” Reed said. “If they took photos, it was occasionally via email. But with that, you don’t have one place where you can go back and look at all the photos.”
When jobs or projects are more complex, documentation becomes even more essential. Real-time visibility helps the office keep track of projects (and find ways to improve them). That’s why Steve and the team introduced Raken's contractor software for small businesses to their field crews.
Raken’s construction app lets field crews complete daily reports, upload photos, and log time cards on the go. Once signed off, reports are uploaded as PDFs to the cloud—so the office can access field data in real time. It’s that simple. And, to Stonwerk’s surprise, all it took was one kickoff meeting for their crews to pick up Raken. No extensive training sessions, no questions asked.
“With Raken, there was no learning curve. We're stone masons, we're not generally known to be really techy guys. And if we can get this technology, anyone can.”
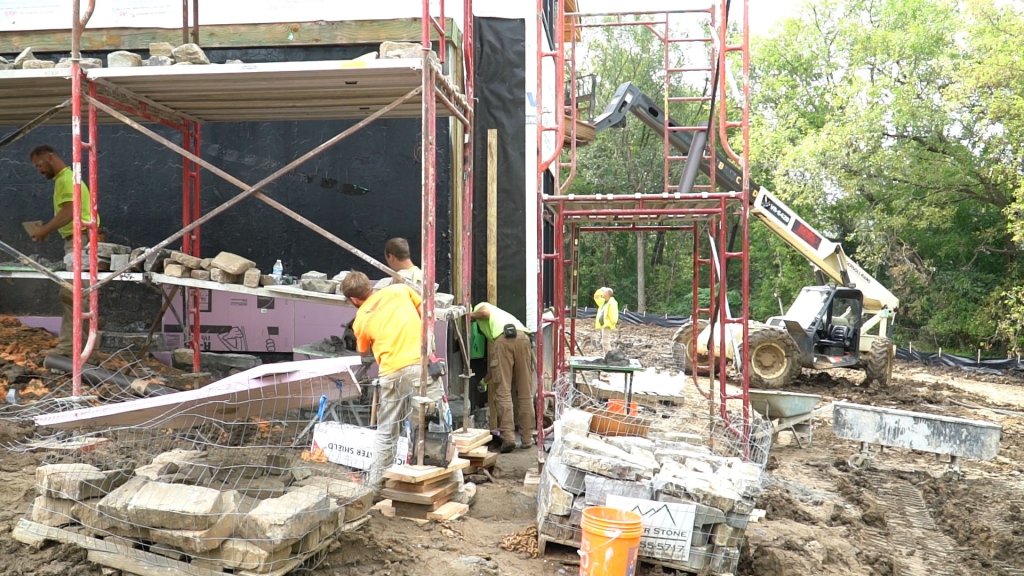
Improving visibility for subcontractors
For subcontractors, finding and keeping jobs is the key to growing business. When you can spot potential problems early, you can run your operation more smoothly. That’s what Pat Redinger, Stonwerk’s Office Manager and Estimator, quickly discovered with Raken’s project dashboards.
“Raken is a one-stop shop for time, comments, and photos. It definitely improves what you know about what's going on with all the jobs, plus it's easy to use.”
Beyond time collection, Raken also helps Stonwerk with invoicing. Photos are stored in one place, making them easy to reference from anywhere.
“When the foremen put the pictures on Raken, I know exactly where they’re at, so I don’t have to drive out to the jobs. I know what the status is, so I know what to invoice for,” Pat said.
How about jobsite safety? Same story. Stonwerk can choose a safety topic from Raken’s digital toolbox talks library, bulk schedule it, and send it right to field supervisors’ phones. Supervisors can even upload sign-in sheets for better, digital documentation.
“Toolbox talks definitely keep us on track, because they’re very structured,” Pat said. “You can load in what you want talked about, and all the crews talk about the same thing that week. Plus, it’s all documented, so we have proof that we did cover a topic.”
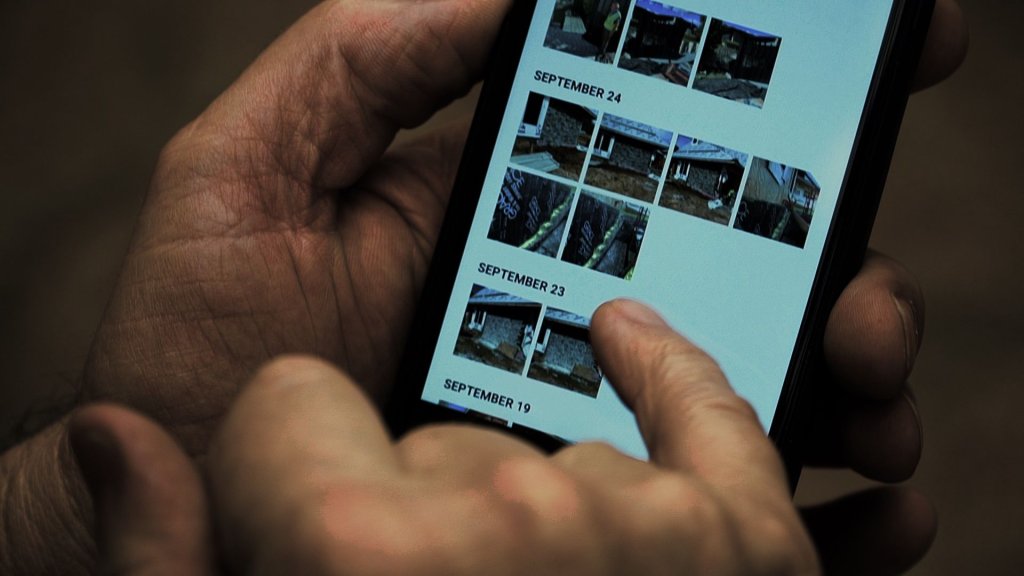
Winning more business with professional reports
For one job in particular, it was Stonwerk’s streamlined reports (made in Raken) that won over the GC. Raken automatically adds photos, notes, and professional formatting to every report. After two other masonry contractors didn’t make the cut, Stonwerk impressed the GC with their time tracking tools and documentation.
“We sent the GC a Raken report to show how we were going to track our time, where every employee has different levels of pay,” said Steve. “After we showed him Raken, there was no question. We got the job—and it ended up being six months’ worth of work. The reports that Raken produces are just so nice, clean, and crisp.”
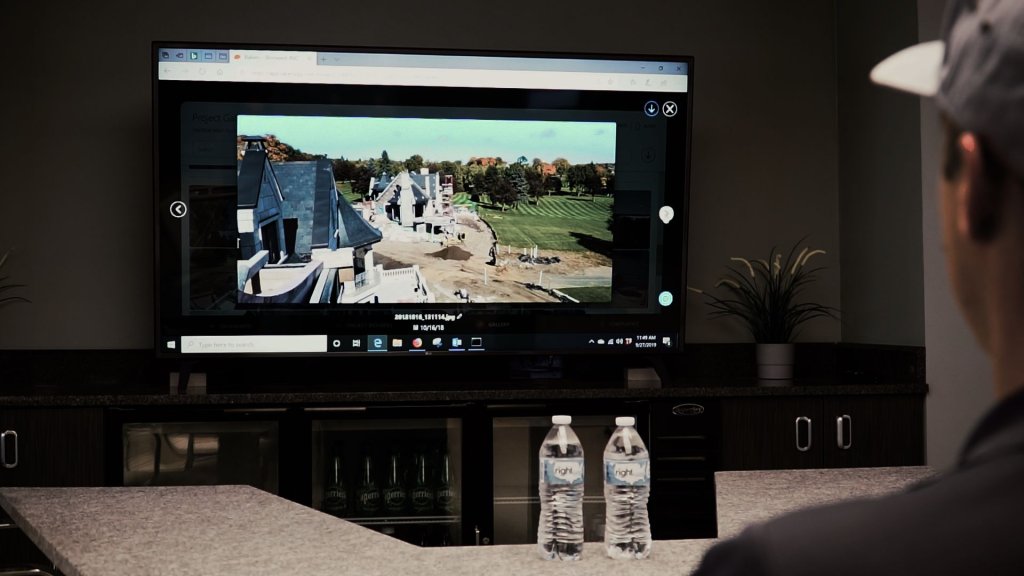
Streamline your field data with Raken
With Raken, Stonwerk modernized their field communication. From daily reports and time cards to time-stamped photos, Stonwerk can improve productivity on the fly—and win more business.
Schedule a demo to see how Raken can improve your field data, just like it did for Stonwerk.