Evolved from lean manufacturing, lean construction is a popular project management methodology.
Learn about lean construction principles and the tools business use to put them into practice.
What is lean construction?
Lean construction is a project delivery method prioritizing operational efficiency. Businesses that follow lean construction principles strive to complete projects with minimal time and material waste and maximum return on investment.
Examples of lean construction practices include reorganizing task schedules to prevent idle time for workers on the jobsite, establishing a review process for purchasing decisions to avoid unnecessary spend, and investing in software to automate time-consuming reporting workflows.
Lean construction principles
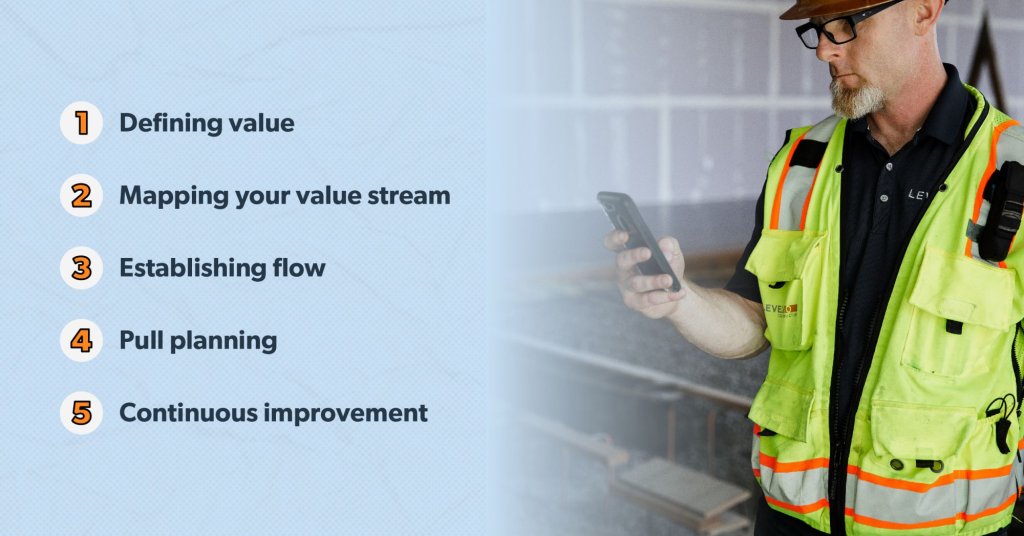
The main focus of lean construction is to optimize efficiency by avoiding unnecessary, unexpected costs.
Lean construction embraces five key principles:
Defining value
Mapping your value stream
Establishing flow
Pull planning
Continuous improvement
These principles are applied throughout the different stages of construction.
1. Defining value
Before construction begins, define a project’s value to the customer. Ask your clients not just what they want built, but also the reasons behind it.
Defining value establishes good client communication and demonstrates a business actually cares about providing a quality finished product. You’ll be able to reference the defined value throughout the construction process to make better decisions that reflect the project’s true purpose.
2. Mapping your value stream
Once you’ve defined value, create a map of your business’s value stream to help better plan your project.
To map your value stream, you’ll need to assess all of the processes you’ll use in order to complete the project. Create a master list and identify which items truly bring value according to the customer’s goals.
The processes that do not add value should be separated into two categories: those that do not add value but are necessary for project completion and those that are unnecessary.
Any unnecessary processes can be eliminated or significantly reduced.
3. Establishing flow
With a map of your value stream, it’s easier to establish a continuous workflow. Break down each necessary process into steps and assess the resources and work hours that need to be allocated.
When you look critically at each step of your workflows, you can reorganize tasks, redistribute labor, and schedule work in the most efficient way possible.
4. Pull planning
Pull planning is a project planning method that involves establishing project milestones and working backwards to determine the steps and timelines needed to accomplish them.
Generally a business will hold a pull planning meeting, gathering representatives from every team involved in the project—including all the subcontractors. These individuals will determine appropriate project milestones and work together to create a plan of action.
By using pull planning, it’s easier to make more realistic schedules and estimates.
5. Continuous improvement
The final principle of lean construction is embracing the fact that no matter how much you optimize, there is always room for improvement.
Even when you’ve applied lean construction principles to a project, unexpected delays can occur, and last minute details are often overlooked or omitted, causing setbacks. Reflect on how a project progressed upon completion to identify ways to improve in the future.
If you acknowledge that there is always space to grow, you can continue to achieve great results through lean construction.
Benefits of lean construction
There are numerous benefits to using lean construction methods. These are the most common advantages:
Save money
Reduce risk
Improve employee morale
Improve customer satisfaction
1. Save money
Working efficiently and effectively is a surefire way to improve project profitability. Using lean construction principles, you’ll save money eliminating superfluous tasks and adopting strategies to avoid wasted resources.
2. Reduce risk
Lean construction techniques reduce risk for your business by helping you better manage projects and create more realistic budgets and timelines
Your projects will start off at a better place, and are more likely to be completed on schedule. You’ll have less chance for disputes and costly litigation.
3. Improve employee morale
Operational efficiency doesn't come at your employees’ expense when you follow lean construction principles. With lean construction, businesses make intelligent, informed decisions to increase productivity without putting an added burden on workers.
Workers will appreciate the elimination of unnecessary tasks and steps, and they’ll be able to focus on tasks that actually bring value to the project.
4. Improve customer satisfaction
Because the lean construction principle of defining value involves establishing good communication with the customer at the beginning stages of project planning, lean construction is more likely to lead to improved customer satisfaction.
The entire construction process begins and revolves around the customer’s defined value. And, as lean construction keeps the project running smoothly, they’ll be more likely to be happy with the finished results.
How Raken helps with lean construction

Raken’s easy-to-use construction management app can help you apply lean construction principles by digitizing your documentation and simplifying complex workflows.
We offer:
Fast, detailed daily reports that are easy to complete and share
Automated production insights
Accurate time tracking
Standardized safety and quality management checklists
Digital forms and document management
With Raken, your team can work smarter, not harder, reducing risk and improving productivity.