What is productivity in construction?
In construction, productivity describes how efficiently a business works. To measure productivity, construction companies closely monitor progress and assess the amount of labor they can typically complete in a given time period.
Because productivity is directly tied to profitability, many businesses invest in production tracking tools and develop strategies to optimize their processes and increase work output.
How to measure construction productivity
There are many different ways to measure productivity in the construction industry. No matter what method you use, the goal of production tracking in construction is to determine whether or not your team is working at a cost-effective and time-efficient rate.
To start, construction companies will look closely at the following metrics:
Costs
Labor input
Material input
Capital input
Energy input
Indirect costs
After recording all costs, work hours, and use of resources in a set time period, the business will compare these numbers against work completed to determine their level of productivity. They will likely combine several different data points for a more comprehensive assessment according to how the business operates.
For example, an electrical contractor may find that, on average, their team takes 65 work hours to rewire each 1200 square ft. of a building. They can then determine if any issues are impacting this number and implement strategies to resolve them. Later, they can conduct another assessment to see if those numbers have changed.
Businesses can track productivity on micro and macro levels, meaning they may focus solely on one project at a time, or even one stage of a single construction project. Or, they may measure productivity across multiple projects at once.
Recommended Read
A Guide to Improving Construction Productivity
Learn how digital production tracking can improve project visibility with accurate data and production insights—all in real time.
The productivity problem in the construction industry
The construction industry historically struggles with productivity.
A 2023 report by the University of Chicago’s Becker Friedman Institute for Economics found that, despite overall economic growth, construction productivity has been in decline for the past several decades.
The report states that while the U.S. economy in general has seen an increase of value added per each full-time (or equivalent) employee, construction has experienced the opposite. Since 1950 through 2019, the amount of value provided by each full-time worker in construction has steadily decreased.
It can be difficult to determine the actual productivity levels of construction companies as a whole, because there are so many different ways to measure value and efficiency. The Bureau of Labor Statistics describes the difficulty of assessing productivity across the entire industry. A 2022 report on the Bureau's website states, “The main challenge to measuring output is that construction projects differ widely in characteristics and features.”
However, the Becker Friedman Institute is confident the statistics are clear. They write, “The productivity struggle within the construction sector is real, and not a result of measurement error.” And, many businesses see the statistics in action.
Productivity is not a new problem for contractors. In 2017, McKinsey Global Institute released a report with similar findings, stating that gross value added per each hour worked in construction had declined even as value per hour worked in other industries like manufacturing was rising.
But, despite the discouraging numbers, there is hope. MGI’s report offered solutions for reworking industry frameworks and managing risks that affect productivity.
Because productivity itself and the way you measure it will differ greatly from business to business, construction companies need to look inward to assess their individual issues and reach resolutions.
Factors affecting construction productivity
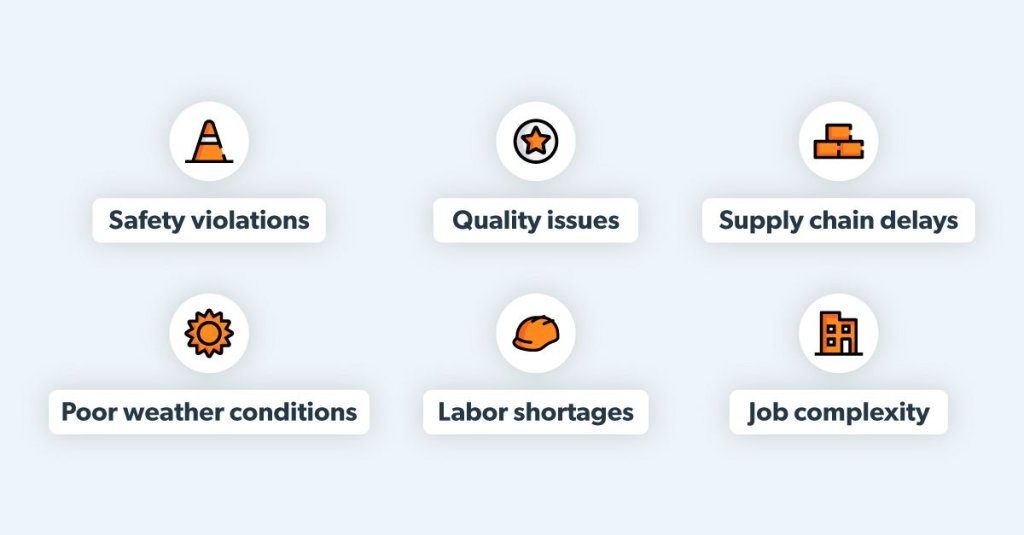
Many internal and external factors affect construction productivity. Any type of delay or change in scope may negatively impact the project budget or schedule.
Some of the most common factors affecting construction productivity are:
Safety violations
Quality issues
Supply chain delays
Poor weather conditions
Labor shortages
Job complexity
Safety violations
A safer jobsite is a more productive jobsite. When the work area is clean, clear, and free of hazards, your crew can work more efficiently with less interruptions.
Establish and enforce good safety practices to improve productivity and help your team focus on project-related tasks.
Recommended Read
The Ultimate Guide to Construction Safety Management
Learn all about construction safety management, including how to use digital tools to prevent injuries and accidents.
Quality issues
Rework is another common reason for delays in construction. Miscommunications, design errors, and other often preventable mistakes lead to quality concerns that need to be resolved before the project can be completed.
You can reduce the likelihood of rework by proactively monitoring for these issues.
Supply chain delays
You may not always get the materials and equipment you need on time. Supply chain issues can be unpredictable.
When materials aren’t available for a specific task, other dependent tasks may also be delayed. It’s important to track your resources.
Poor weather conditions
Extreme weather conditions can prevent work from proceeding as scheduled.
Depending on the location of the project and the time of year, you may need to build time for weather concerns into the work schedule.
Labor shortages
There is currently an industry-wide labor shortage in construction. If you’re short-staffed, you may not be able to work as efficiently as you could normally.
The exact skills, experience, and qualifications of your crew will also affect productivity.
Job complexity
Certain projects are more inherently risky than others. Productivity is more difficult to predict when the job is especially large, complex, or dangerous.
Assessing the risk level of a job will help you determine whether or not you should expect a change in your average productivity levels.
Recommended Read
The Ultimate Guide to Construction Risk Management
Learn how to create a risk management plan for your construction projects.
How to improve construction productivity
With all the factors that impact how efficiently you work, improving—and even maintaining—productivity in construction can be difficult.
These tips will help you mitigate risk factors and make sure your team stays as productive as possible.
Be thorough in the planning and design stages
Provide adequate training to employees
Focus on safety
Follow best supply chain management practices
Use construction productivity software
1. Be thorough in the planning and design stages
Investing extra time in the pre-construction phase of a project is one of the best ways to prevent inefficiencies later on.
Creating a project budget and schedule are critical tasks that require great attention to detail. Use historical data to plan projects as accurately as possible based on your team’s past performance.
You should also make sure to review all designs thoroughly before the construction phase begins to catch errors that could lead to disputes or quality issues.
2. Provide adequate training to employees
Every business uses different processes. Without adequate training, your employees may fail to adopt optimized workflows, creating unintentional roadblocks.
Make sure your employees fully understand the procedures you use for completing work, monitoring safety, and communicating in the field. Empower them to implement the strategies you’ve created from the top down.
3. Focus on safety
When employees feel safe and protected on the jobsite, they can focus on completing the work that’s assigned to them without having to worry about potential accidents. When you prioritize safety, you’ll also reduce the risk of violations that cause significant delays to the project schedule.
Keep safety policies top of mind by giving your employees access to checklists, observations, and toolbox talks that cover relevant topics.
4. Follow best supply chain management practices
While supply chain issues aren’t always under your control, you can prepare for them by following best practices.
Get familiar with common resource management challenges, like inventory miscounts, and research ways to work around them. Track material use closely and place orders for new supplies well in advance if you think you may run out in the middle of an active project.
Plan ahead when scheduling tasks to avoid delays and develop good working relationships with your suppliers.
5. Use construction productivity software
Construction productivity software helps businesses better track material use, log work hours, and communicate jobsite progress than using pen and paper. With more accurate insights, you can pinpoint areas for improvement and plan bids that accurately reflect your capabilities.
Construction productivity tracking software

To stay competitive, modern construction companies often use some form of digital production tracking.
There are many options for construction productivity tracking software on the market. Decide what tools are best for you by making sure your software can help you accomplish the following goals.
Collect more detailed production data
Without detailed data, creating bids and project schedules is an educated guess at best. Productivity tracking software makes data collection easy.
Field crews will typically be able to capture progress updates and submit them directly from the field, entering work hours, material use, and other production information using mobile data capture. They can more easily provide a higher level of detail without reporting taking time away from other responsibilities.
To make reporting even easier, you can use software to create report templates, checklists, and time cards that are tailored to your business’s processes. Track progress in a standardized way and be sure your crew meets your exact reporting requirements.
Automatically analyze productivity
Instead of manually organizing and analyzing productivity data, construction production tracking software can save you time by automatically taking information submitted via the field and visually demonstrating how actual performance is measured up against estimates.
Some software will create charts and graphs tracking productivity and showing you at a glance where you are saving and wasting the most work hours.
Use these automated insights to quickly make informed decisions about scheduling, purchasing, and hiring.
Maintain clear documentation
When you aren’t tracking production in a streamlined way, saving that data for future use quickly becomes a challenge. Whether you have a physical file cabinet of past reports or separate spreadsheets saved across multiple devices, locating the information you need later to plan future projects may take hours.
With digital production tracking, documentation can be automatically saved in organized project-specific folders in the cloud. When it’s time to review your strategies or draft a new bid, use digital search to quickly find the right documentation to help you through that process.
Prevent delays and reduce risks
Construction productivity tracking software should allow you to monitor production in real-time. Not only will you be able to make more proactive decisions, you’ll also catch potential safety, quality, and supply issues early, so you can pivot before these concerns develop into catastrophes.
Reducing risk is the most effective way to improve productivity, and software helps you do so more consistently.
In conclusion…
All businesses strive to work efficiently, but with the industry’s tight profit margins, developing strategies to improve productivity is especially important in construction. The first step to increase productivity is to analyze current performance.
In order to accurately measure productivity and identify areas for improvement, many construction companies use production tracking software. Software helps improve data quality and can save time by automatically organizing data into actionable insights.
And, once strategies to improve productivity are put in place, software helps construction companies continue to monitor their impact.
Automate productivity tracking and gain insights faster
Our production tracking software offers easy-to-use mobile reports, checklists, and automated dashboards that help busy contractors analyze productivity at a glance. Accurately track time and materials and collect, share, and publish detailed field data with a click or a tap.