For contractors, safety is serious business. An effective construction safety management system greatly reduces the risk of incidents and injuries.
What is construction safety management?
Construction safety management is the process businesses use to proactively mitigate safety risks and reduce the likelihood of incidents, injuries, and fatalities on the jobsite.
The main goal of construction safety management is to establish best practices for identifying and resolving potential violations. A construction safety management system typically combines multiple strategies and may include tools that help field and office teams better report, monitor, and analyze safety data.
What are the benefits of construction safety management?
The main benefits of practicing good safety management in construction are:
Safer jobsites
Higher productivity
Fewer disputes and litigation
1. Safer jobsites
The most obvious reason safety management is important is because it helps construction companies protect their most valuable assets: their employees.
Tens of thousands of contractors are injured onsite every year in the U.S. A business is responsible for providing as much protection for their workers as possible.
Tens of thousands of contractors are injured onsite every year in the U.S.
With the right tools and strategies, you’ll empower your employees to work more safely and reduce the chance of themselves or their coworkers getting hurt on the job.
2. Higher productivity
Safety violations can slow down progress and lead to costly project delays. Whether a violation itself causes inefficiencies or it results in an incident that shuts down activity in the work area for any given time, safety issues often negatively affect productivity.
The best way to avoid those delays is to catch and correct issues quickly.
3. Fewer disputes and litigation
Safety related disputes and litigation may seem inevitable in construction, but good safety management practices will help you reach a fast, fair resolution—or avoid legal issues entirely.
Having an established construction safety management system reduces the risk of incidents that commonly lead to disputes and litigation.
Good safety management practices can also help you improve documentation. You’ll be able to clearly demonstrate you’ve followed proper procedures and fulfilled the necessary requirements.
Recommended Read
What is Construction Litigation?
Construction litigation can be costly and time-consuming for all parties involved. Learn what causes it and, most importantly, how to avoid it.
Four pillars of a construction safety management system
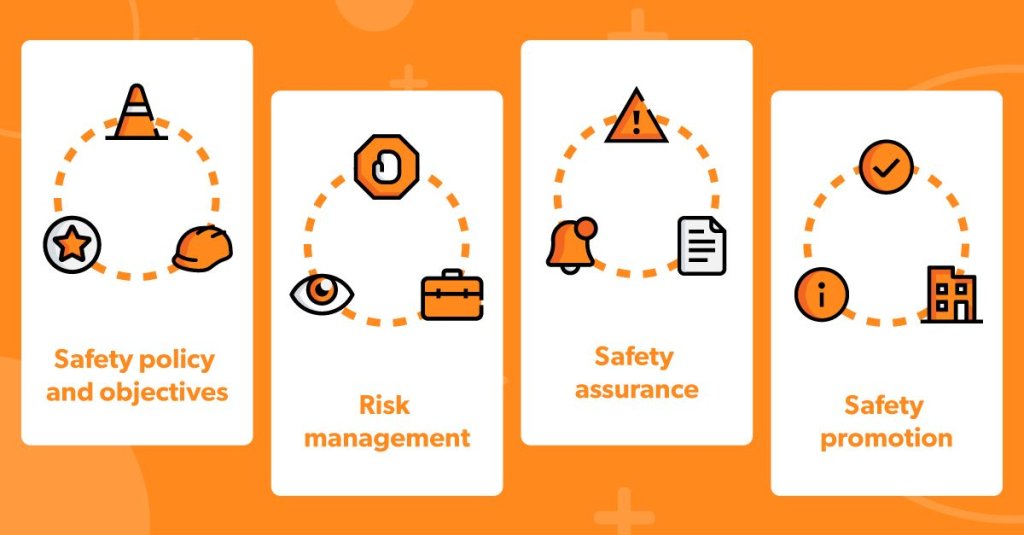
According to OSHA, the four pillars of construction safety management are:
Safety policy and objectives
Risk management
Safety assurance
Safety promotion
1. Safety policy and objectives
No safety management strategies can succeed without effective communication. Formalize your safety policies and procedures with written documentation to clearly communicate expectations and obligations to your employees.
Outline all important policies, procedures, objectives, and roles and distribute these documents to employees in an easy-to-access format. Have employees sign off on their receipt and understanding of the information and make sure to repeat the process whenever there is an update or new addition.
2. Risk management
How will your business proactively assess and monitor safety risks?
A construction risk manager, safety manager, or other stakeholder will typically review each project and determine the highest risk factors. They’ll weigh both the likelihood of each identified risk and its potential impact.
Then, they’ll organize the risks into different categories that reflect priority. High priority risks are risks that are likely to occur and lead to major negative outcomes, while low priority risks are less likely to occur and may only have minor effects. Construction companies should focus more time and resources on mitigating high priority risks than low priority ones.
For example, you may review a project that requires extensive roofing work. In this case, falls are a high priority safety risk. To properly manage that risk, a safety manager will create a plan to ensure all employees are informed of proper roofing safety procedures, are equipped with the right protective equipment, and have the tools they need to closely monitor for safety violations when work begins.
While the larger list of risks associated with each project may include financial, legal, environmental, and project related risks, safety violations are a constant risk factor in construction. Every project will likely come with some safety risks, and your construction safety management system should provide guidelines for assessing and mitigating them.
Recommended Read
The Ultimate Guide to Construction Risk Management
Learn how to create a risk management plan for your construction projects.
3. Safety assurance
It’s not enough to put risk management plans in place. Monitoring how they work in the field and adapting as needed is the third pillar of safety management.
Your field crews should consistently report on safety data. Keep track of common violations. Gather as much information as possible about the cause behind any incidents and determine whether or not safety procedures were sufficiently observed.
Use this information to assess what strategies are successful and identify areas for improvement.
4. Safety promotion
Finally, make sure your employees feel engaged and involved by providing frequent safety training and incentives for them to take accountability for safety management in the field.
Consider investing in software and devices that help them more easily conduct inspections, capture data, and report concerns.
What does a construction safety manager do?
A construction safety manager, also referred to as a construction safety officer, is a designated employee responsible for defining and implementing safety management strategies at a construction company.
Depending on the size of the company, they may employ one or more full-time construction safety managers. Smaller businesses may split safety management responsibilities between different stakeholders.
What are a construction safety manager’s responsibilities?
Construction safety managers:
Draft policies, procedures, and other safety documentation
Review bids and projects to assess safety risks
Create risk management or risk mitigation plans
Create, assign, and review safety checklists and observations
Monitor project progress
Conduct site inspections and inspect tools and equipment
Conduct investigations of incidents and near-misses
Respond to employee safety concerns
Provide employee safety training
Assess and implement construction safety software and digital safety tools
Enforce regulatory guidelines
These are not the only responsibilities a construction safety manager may have. Safety plays a part in nearly every stage of the construction process, so safety management is a complex role that can vary depending on the needs of the business.
Construction safety manager training
There are many degree and certification programs for construction safety management.
While you don’t always need formal education to qualify for this role, completing a certification program is a great way to grow your resume and learn about the newest safety strategies and technologies available. Some certifications can be obtained in a short period of time through focused courses.
Often, businesses favor applicants with a blend of education and industry experience.
Construction safety manager certification programs
B.S. Occupational Safety and Health – Construction Safety - Columbia University
Safety & Health Fundamentals Certificate Program for Construction - OSHA
Certified Safety Manager: Construction (CSMC) - National Association of Safety Professionals
Safety Management Certificate Program - American Society of Safety Professionals
Safety Management Training Course - The Construction Association
This is only a small sample of available programs that can be completed online in any location. You may be able to find an in-person program in your area.
Construction safety manager salaries
Construction safety manager salaries vary by location and experience level.
As of July 2023, Glassdoor lists the average salary for this role as $94,417, while the median salary for construction safety managers is $114,730 according to Salary.com. According to Indeed, the average base pay is $83,317.
Construction safety manager jobs
You can search for construction safety manager job openings using online career sites and speciality job boards.
Construction safety management tips
Because safety is so important, drafting a safety management plan for your construction business can be a daunting task. Keep these tips in mind to help you get started :
Get all employees involved
Plan ahead
Do your research
Create checklists
Use construction safety management software
1. Get all employees involved
Even if your company is large enough to hire one or more dedicated safety managers, safety in construction isn’t ever just one person’s responsibility.
Encourage all employees to take an active role in incident prevention. Schedule frequent toolbox talks and provide resources that help them keep safety constantly top of mind and easily report issues.
Consider offering incentives for positive behavior, like wearing the proper PPE or keeping the work area clean and tidy.
2. Plan ahead
Always remember that the best way to mitigate the risk of safety incidents is to avoid the violations that typically lead to accidents and injury in the first place.
When reviewing project risks, be thorough and critical. Try to think of every possible scenario that could go wrong and create both a plan for preventing or avoiding that risk and plan for responding if an incident does happen.
Allocate time for risk mitigation in every project schedule. While it’s difficult to start addressing safety risks with this level of detail,, the more experience you have creating mitigation plans, the easier the process will become.
3. Do your research
Keep up-to-date with OSHA recommendations and periodically review your safety practices to make sure you meet the latest standards.
OSHA is the national Occupational Safety and Health Administration. The guidelines they set can provide a great starting base for your own safety policies. If you model your policies after OSHA standards, you can be sure you’re meeting government regulations and can about costly fines in the event of an inspection.
You can also attend industry events, webinars, and training to network with your peers and learn how they approach safety management.
Recommended Read
How to Prepare for an OSHA Inspection in Construction
The best way to prepare for an OSHA inspection—or avoid one entirely—is to proactively establish, enforce, and document good safety practices.
4. Create checklists
Construction checklists are simple yet effective safety tools. Create checklists for inspections and safety monitoring tasks and assign them to be completed by field crews as a part of daily labor.
Employees can use checklists to make sure they don’t miss any critical steps in safety procedures.
5. Use construction safety management software
Today’s construction companies use technology to aid almost every construction process, and safety management is no exception.
Using pen and paper or individual documents to implement procedures and policies is time consuming and can quickly become disorganized. Many software solutions are designed to improve safety in a much more efficient way.
Construction safety management software
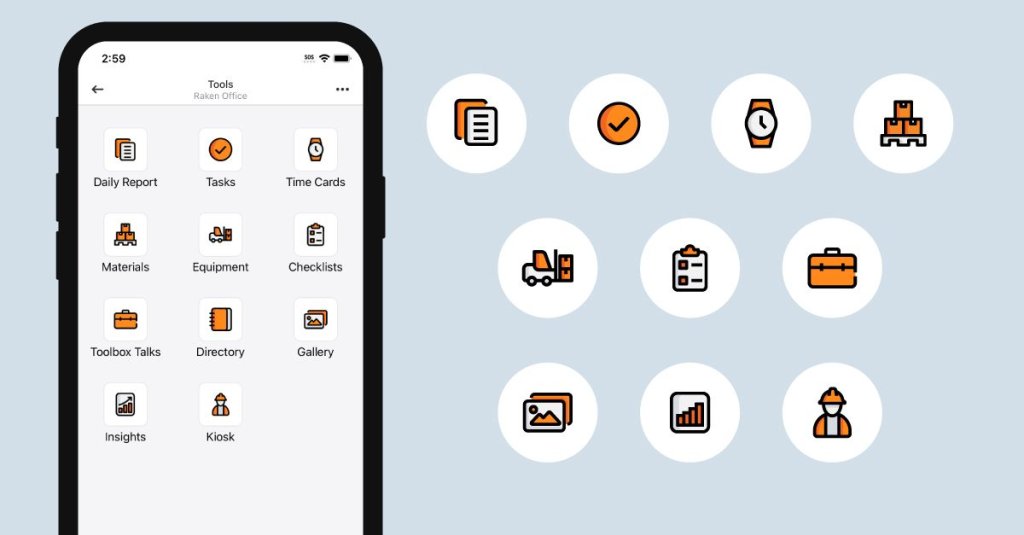
Investing in construction safety management software makes implementing the strategies listed above a faster, more streamlined process.
However, different software providers offer various features and benefits, and some focus primarily on a single functionality like toolbox talks or incident reporting while others are used solely for organizational purposes like document management.
To make the most of your investment, look for a comprehensive platform that allows you to capture, share, analyze, and store safety data across all your projects seamlessly.
The ideal solution will include the following features.
Managed checklists
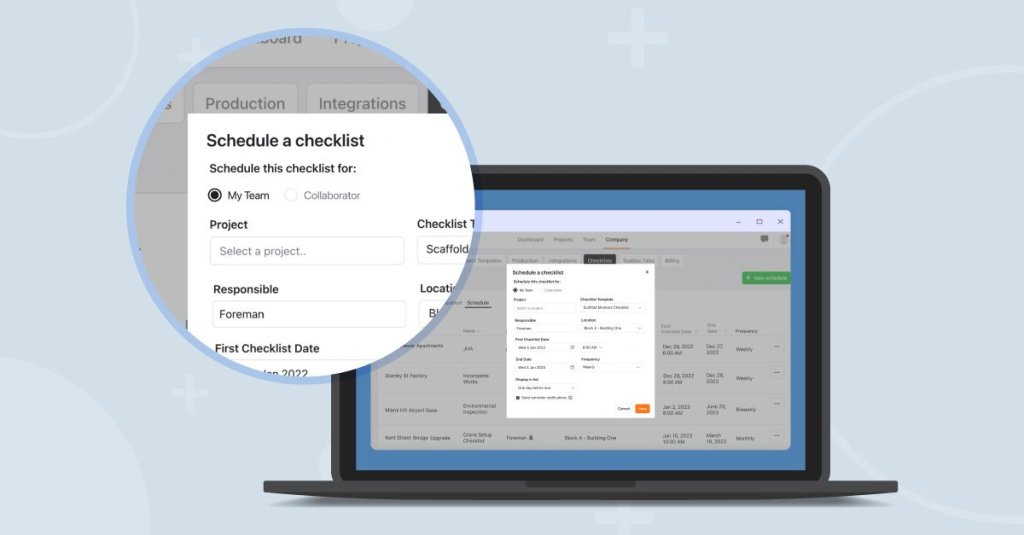
Your construction safety management software should allow you to create custom safety checklists and assign and schedule them. Then, assigned crew members can quickly complete checklists in the field via mobile device.
Remember that, while they’ll provide greater detail, digital checklists should be less time consuming and more reliable than pen and paper. Choose software with a clean, easy-to-use design —overly complex tools can be counterproductive.
You may even be able to automate workflows and set up notifications to automatically inform assignees when checklists are due and help stakeholders monitor progress.
If you prefer to use pre-made checklists, some safety software solutions provide a library of templates you can use right away or easily customize.
Observations
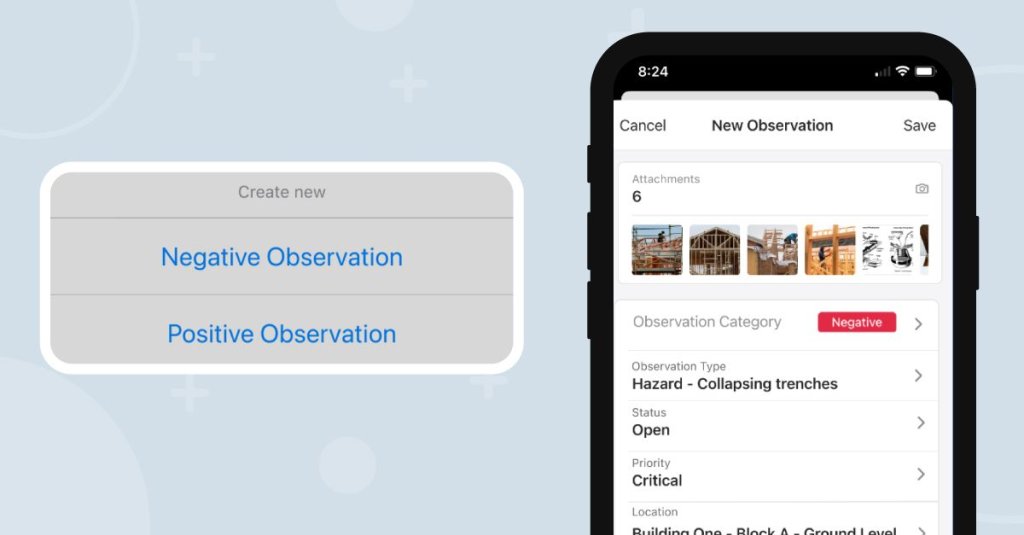
Safety management software should allow for field observations to be submitted independently or attached to checklists when more information is needed. The process for doing so should be easy-to-follow and include steps for adding all the relevant details.
It’s helpful when the person submitting the observation can directly assign individuals to resolve any issues. They should also be able to tag additional personnel for awareness, so that both the submitter and key stakeholders can track the observation’s resolution and escalate the issue if needed.
Toolbox talks
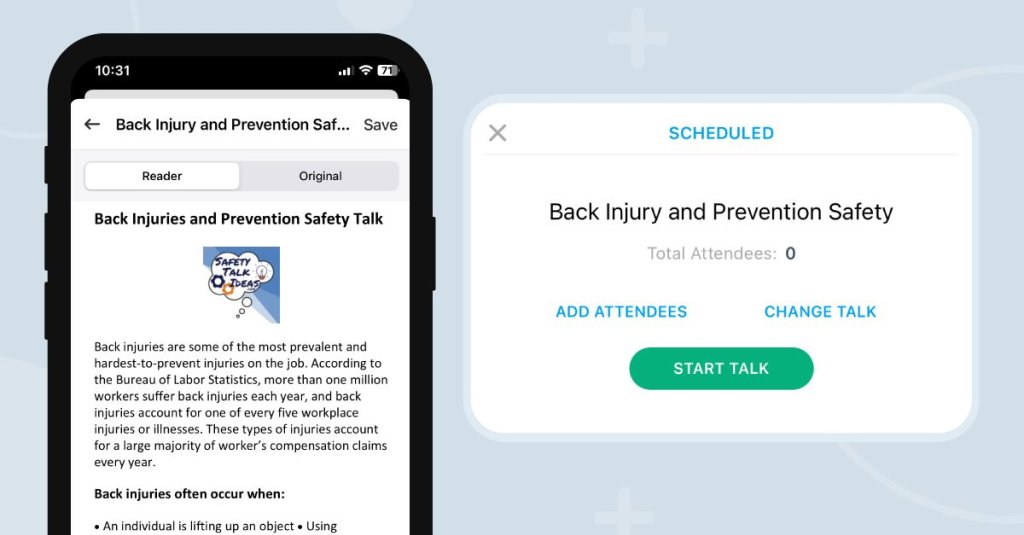
Construction safety management software should include toolbox talks. Having access to a built-in library of talks that you can schedule saves time for safety managers, who won’t have to spend valuable work hours searching for high quality talks each time they need to deliver one.
You should also be able to digitally document attendance and organize sign-in sheets in your secure digital storage system.
Photo and video documentation
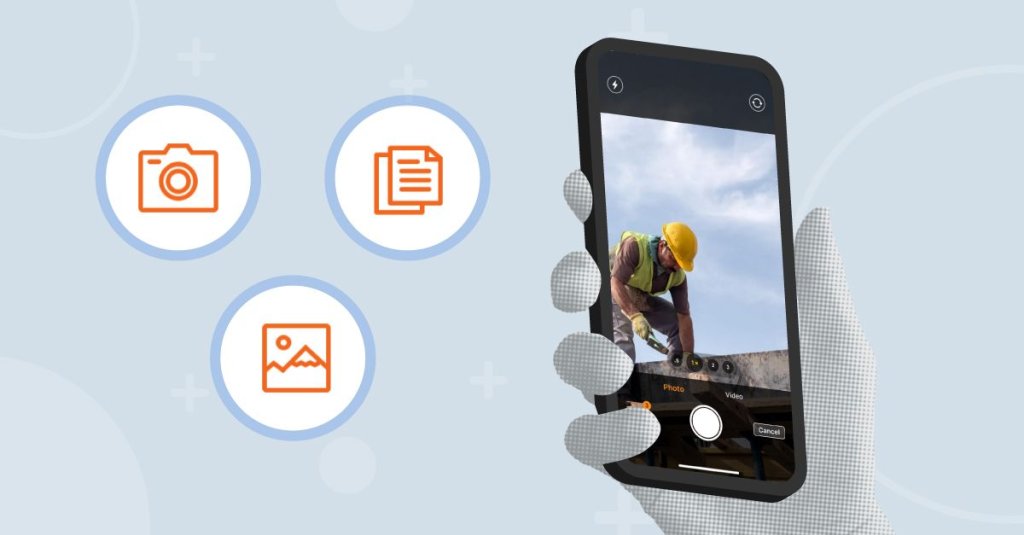
The ability to add visual data to checklists and observations is highly recommended. Photos and videos provide added clarity and help offsite stakeholders identify safety issues that can’t be easily communicated in writing.
Any photos and videos captured using your safety management software should have automatic time and date stamps.
Automated safety insights
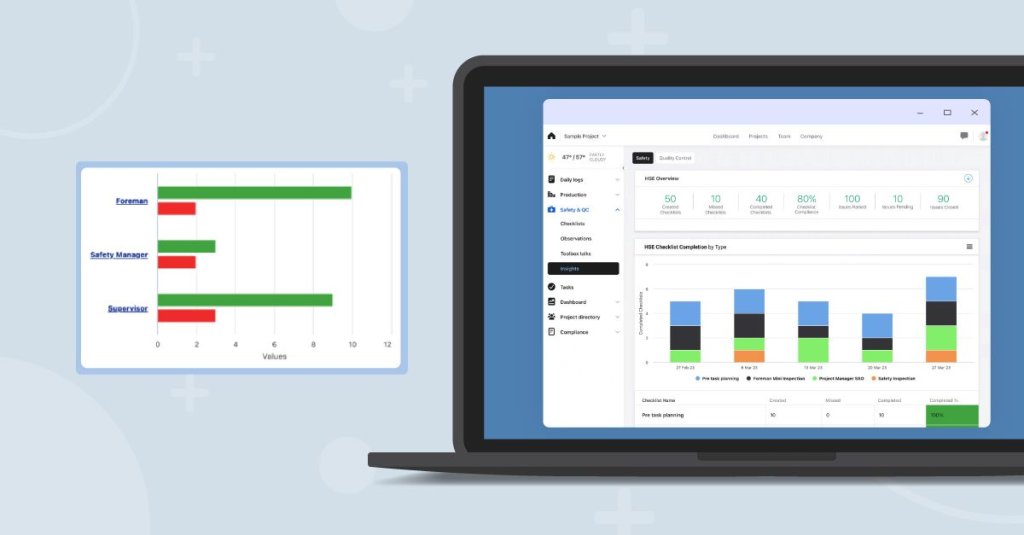
Software that automatically organizes and analyzes safety data collected through checklists and observations helps you gain actionable insights faster.
Consistently track your safety management system’s performance with dashboards and reports that visually demonstrate KPIs and safety trends. See how your team is measuring against goals, identify common violations, and adjust your strategies in real-time to improve compliance and stay productive.
In conclusion…
With all the risks involved in construction, safety should always stay top of mind. To protect your workers and your business, implement a safety management system that includes documented policies and procedures, risk management strategies, safety assurance, and safety promotion.
For maximum efficiency and effectiveness, make construction safety management software a part of your process. Digital tools improve documentation and help your crew follow safety procedures without adding extra stress to the workday.
All your construction safety tools in one place
With streamlined checklists, observations, and toolbox talks, Raken makes construction safety management easier than ever. Quickly report and resolve issues and analyze safety data at a glance.