Toolbox talks are an important safety strategy, but they're sometimes treated like an afterthought on the jobsite.
This guide will teach you how to deliver better toolbox talks that educate and engage your employees.
What is a toolbox talk?
Toolbox talks are brief, casual safety meetings. They help supplement formal training from the Occupational Safety and Health Administration (OSHA).
Some are short, 5-10 minute refreshers on best practices. Others are more in depth, introducing employees to new procedures or updated guidelines.
Construction companies may refer to toolbox talks as tailgate meetings, safety briefings, pre-starts, or other names.
Why are toolbox talks important?
Toolbox talks are important because they protect field crews and prevent accidents.
While OSHA doesn't define specific rules for the exact content and frequency of toolbox talks, most construction companies conduct them on a regular basis to cover all safety training requirements.
Toolbox talks help employers make sure their staff are equipped with the tools and information they need to safely perform their job responsibilities.
Toolbox talks are important because they protect field crews and prevent accidents.
Common safety violations in construction
Toolbox talks combat some of the most common safety hazards in the construction industry.
According to OSHA in 2021, the top 10 most frequently cited safety violations involved:
Fall protection
Respiratory protection
Ladders
Hazard communication
Scaffolding
Fall protection training
Control of hazardous energy (lockout/tagout)
Eye and face protection
Powered industrial trucks
Machinery and machine guarding
This means that field workers often failed to follow proper guidelines to protect themselves against falls, respiratory damage, and eye and face injuries. They also neglected safety procedures when working with ladders, scaffolding, powered and industrial trucks, and other equipment.
Mitigating risk with toolbox talks
In 2021, the Center for Construction Research and Training reported that the leading causes of fatal injuries in construction were falls, electrocutions, and accidents caused by being struck by or caught in between equipment-directly corresponding with many of the items on the list of most frequently reported violations from that same year.
While not all incidents are the result of violations, it's clear that construction companies have a responsibility to establish and enforce strict safety procedures that prevent serious injury and death.
Toolbox talks give managers the opportunity to provide timely, relevant reminders to their employees. Is your crew currently working with ladders? Schedule a refresher on ladder safety. Or, have they recently been misusing personal protective equipment (PPE)? It's time to review best practices.
Formal training often needs to be scheduled weeks or even months in advance. Toolbox talks are flexible and, in a few short minutes, can prevent major issues onsite due to forgetfulness or neglect.
How often should toolbox talks be carried out?
The occupational safety and health professionals at OSHA recommend construction companies hold toolbox talks on a daily or weekly basis depending on the business's needs and resources.
More frequent toolbox talks lead to less incidents. Statistics from a 2020 report by Associated Builders and Contractors confirm companies that conducted daily toolbox talk meetings reduced Total Recordable Incident Rates (TRIR) by 82% over companies that held them monthly.
Whatever frequency you establish, talks should be conducted at the start of the workday or beginning of each shift.
Statistics confirm daily toolbox talk meetings reduce Total Recordable Incident Rates (TRIR).
How to conduct a toolbox talk
To conduct an effective toolbox talk, construction managers need to choose a relevant topic, prepare the content, schedule the talk, deliver it, and document attendance.
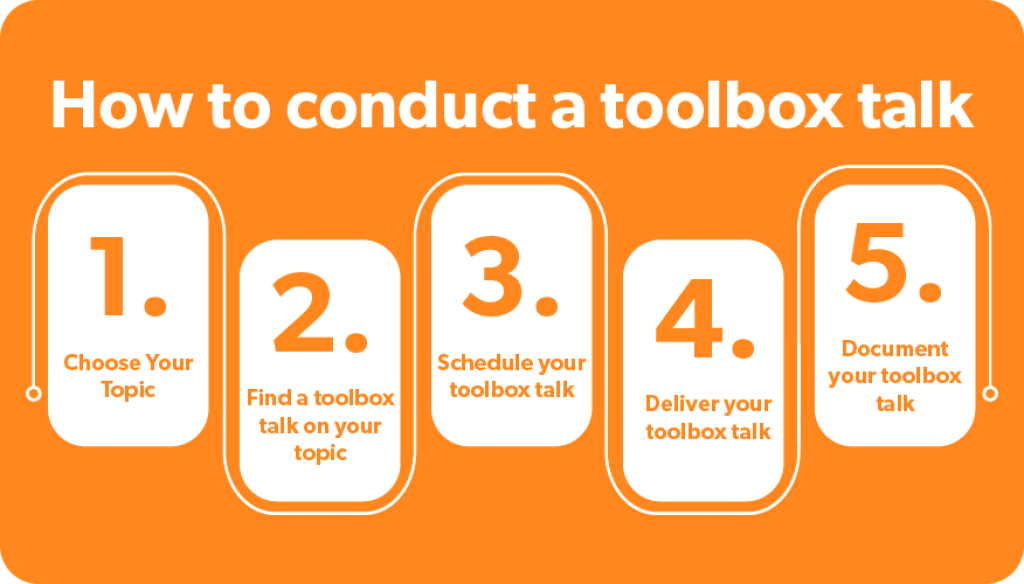
1. Choose Your Topic
Think critically about your team's current projects and choose a relevant topic that applies to upcoming tasks. Or, use a toolbox talk to address any recurring safety issues. Remember that you can cover the same subject twice, especially if it's an area you've identified for improvement. Don't be afraid to split a topic into several toolbox talks to examine it in great detail.
If you've already covered the most relevant topics based on current work or past violations, consider choosing universal subjects like hazard reporting or workplace inspections.
Toolbox talks can be used to teach these general skills that help employees properly identify and quickly respond to safety issues. Or, they can be highly specific.
2. Find a toolbox talk on your topic
Most construction managers aren't professional public speakers, and even if they are, they don't have time to create new toolbox talks from scratch each morning. You'll need to find a prewritten talk that is clear, thorough, and best addresses your major concerns.
Some managers search for free toolbox talks published on the internet, while others have access to digital toolbox talk libraries or physical copies kept on file.
3. Schedule your toolbox talk
After you've chosen a topic and prepared your content, you need to schedule your toolbox talk. Choose a convenient time and clearly communicate the details to your employees well in advance.
Make sure your team understands the importance of the talk and explain why attendance is mandatory.
4. Deliver your toolbox talk
When it's time to deliver your toolbox talk, make sure you are respectful of the scheduled start and end time. Read the talk and give your employees the opportunity to discuss key points or ask questions.
Recommended Read
Five Tips for Effective Toolbox Talks
Explore more techniques for giving better toolbox talks.
5. Document your toolbox talk
Document attendance and keep a consistent record of toolbox talk dates and subject matters for easy reference.
This can help you avoid duplicate talks when choosing future topics and protects your company against risks by proving you've made the effort to provide ongoing safety training on a regular basis.
Use our free toolbox talk sign-in sheet template to get started!
Toolbox talks topics
The most popular toolbox talk topics deal with safety issues commonly experienced on the jobsite. These include:
Fall protection
Accident and injury prevention
Equipment safety
Weather safety
Inspections
Fall protection toolbox talks
Fall protection toolbox talks provide prevention guidance and tips for avoiding serious injury if a fall does occur.
Talks may focus on slips and trips that occur as the result of a spill or physical hazard, or be geared towards falls from ladders, scaffolding, elevated platforms, and other equipment.
Accident and injury prevention toolbox talks
Accident and injury prevention toolbox talks cover a wide variety of topics. They may focus on specific accidents and injuries in detail or demonstrate general prevention techniques.
For example, they may offer universal guidance on pinch points, spotter safety, and situational awareness or deal explicitly with back injuries, lacerations, or electrocutions.
Equipment safety toolbox talks
Some toolbox talks are all about safe and proper use of construction equipment. Any tool large or small may be the focus, including hand tools, vehicles, and heavy machinery.
Weather safety toolbox talks
Special precautions should be taken when certain weather conditions affect the jobsite.
Weather safety toolbox talks provide guidelines to keep workers safe and healthy in rain, snow, extreme heat, and other environmental circumstances.
Inspections
Toolbox talks can outline proper procedures for workplace and equipment inspections.
Where to find free toolbox talks
You can find many free toolbox talk resources online. However, some free sites don't offer an extensive list of topics, or their content is unclear or outdated.
Here are the best free toolbox talk resources available:
Remember that when you choose a talk, you should always review the content before you deliver it to your team. That way, you can be sure the information is relevant and meets current standards.
Toolbox talk software
If you're searching online for a new toolbox talk each week, you're spending a significant amount of time browsing, downloading, and printing or saving topics.
Then, you've got to separately record attendance and find a way to securely store that information and keep track of which topics you've covered.
Toolbox talks should be simple, but without the right tools, preparing, delivering, and documenting them can quickly become unmanageable. Consider investing in toolbox talk software that simplifies and streamlines your process.
The main benefits of toolbox talk software
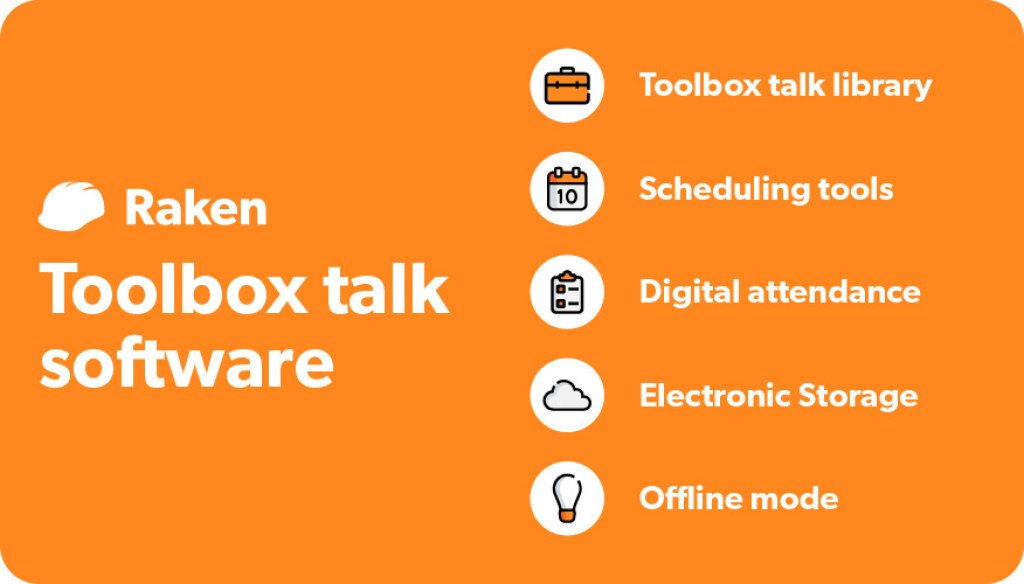
The main benefits of toolbox talk software are ease of use and consistency.
Having dedicated toolbox talk software means no more searching for topics online. Instead of downloading and saving or printing PDFs, you can access talks directly in your software.
The different features of toolbox talk software
Good toolbox talk software will include the following features:
A ready-to-use toolbox talk library - The meat of any toolbox talk software should be an extensive library of appropriate topics. The content of each talk should be well-written, comprehensive, and clear.
Customization options - You should be able to upload your own toolbox talks to the existing library or make changes to pre-written talks if needed.
Scheduling tools - The most useful toolbox talk software will also include scheduling features that allow managers to schedule talks within the software and automatically notify employees.
Attendance documentation - Some software accommodates electronic sign-ins. Managers can track attendance using a tablet or mobile device instead of pen and paper.
Electronic storage - Both the talk details and attendance should be stored electronically via cloud storage, which makes for easy reference and review.
Offline mode - Sometimes you can't get service on the jobsite. Make sure any toolbox talk software you choose can also be accessed offline.
There are many toolbox talk software options on the market. Carefully review a potential provider's capabilities before making a decision.
And, instead of needing careful review in advance, you can be confident in the accuracy and consistency of toolbox talk content.
The main benefits of toolbox talk software are ease of use and consistency.
Toolbox talk best practices
What makes a good toolbox talk? We've already established that talks should be thorough and easy-to-understand, but what does that look like in practice?
They may vary in structure depending on the subject matter, but a good quality talk will always address the following questions:
What is the talk about?
Why is this topic important?
Who does this information apply to?
What are common mistakes or misinterpretations?
What is the talk about?
Briefly introduce the audience to the subject matter and clearly define the talk's purpose.
This will engage your audience and give them a heads-up about what this toolbox talk meeting should accomplish.
Why is this topic important?
Explain to your audience why they should pay attention to the talk. You can include statistics or examples of accidents and injuries that occur when the guidelines covered aren't followed.
Who does this information apply to?
Give specific examples of how your audience can apply the talk's information to their individual daily tasks.
What are common mistakes or misinterpretations?
List common violations or misunderstandings related to the talk topic. Some employees need concrete examples before they realize they've been misinterpreting the rules.
Recommended Read
Toolbox Talk Example
See what a toolbox talk on workplace inspections looks like.
The tradition of safety
The history of toolbox talks is unclear, but as the National Precast Concrete Association finds, the term has been in use since at least the 1940s. And well before we started referring to these meetings as toolbox talks, contractors have always shared responsibility for keeping each other safe on the jobsite.
Construction is one of the largest industries in the world, and also one of the most dangerous according to the National Safety Council. While stricter regulations and growing knowledge have led to improvements in the functionality and reliability of both personal protective gear and construction equipment, working as a field contractor remains a risky profession even in modern times.
As the risks remain, toolbox talks have been and will continue to be a necessity.
In conclusion...
OSHA may not specifically require construction companies to deliver critical safety education in the toolbox talk format. But, there is no easier, more flexible way to meet all your training obligations.
Keep field crews safer and empower them to protect themselves and their coworkers from accidents and injury with consistent, relevant toolbox talks. Customize talks to best fit the needs of your current projects, and be sure to document both the topics covered and attendance records for future reference.
Better toolbox talks, less work
With our built-in library of toolbox talks plus in-app scheduling and attendance, Raken helps your crew stay safe while saving time.