Blog
Catch up on all the latest construction tips, news, and updates.
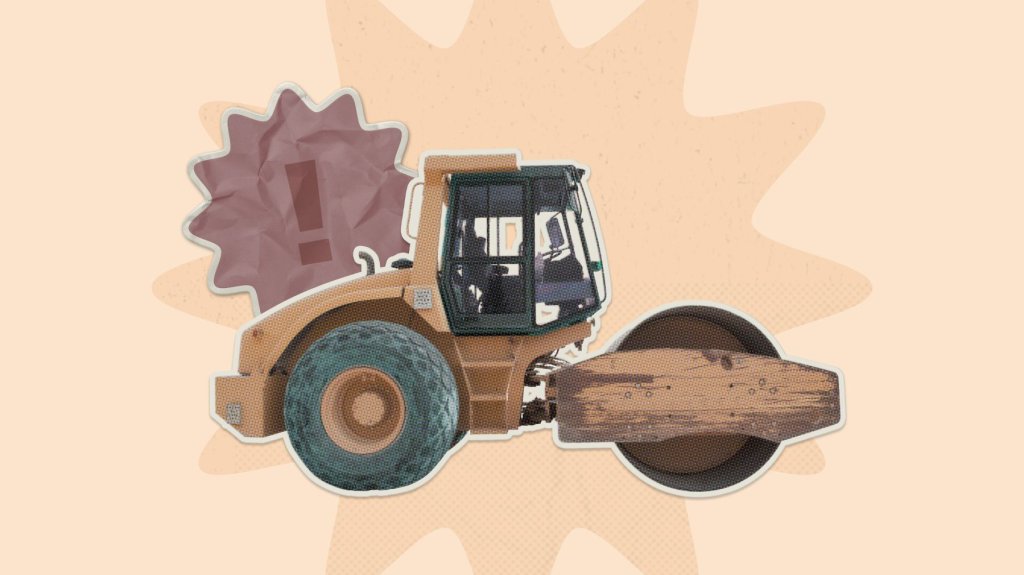
Three Common Construction Equipment Mistakes (and How to Avoid Them)
How you manage your equipment makes a big difference. And some of the most common mistakes in equipment management are also the easiest to avoid.
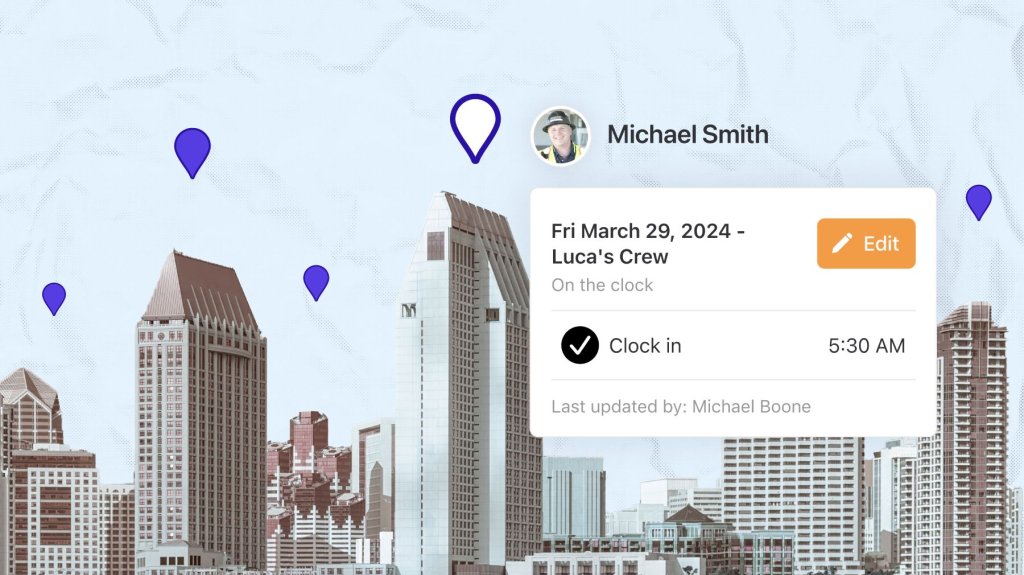
What is Construction Workforce Management?
Just like materials and equipment, your workforce is a valuable resource that needs effective management.
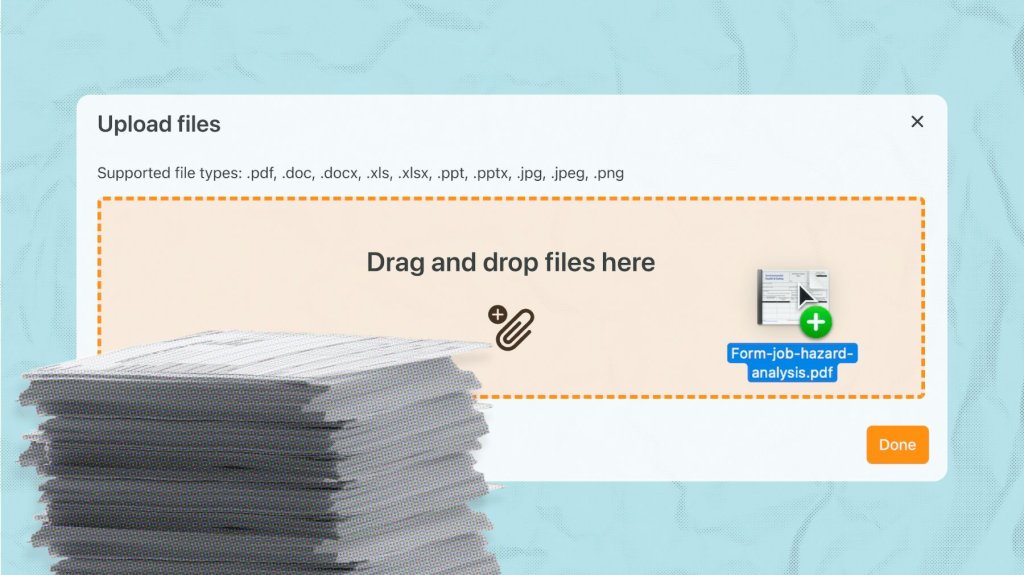
How to Reduce Paperwork in Construction
Going paperless in construction is easier than you think.
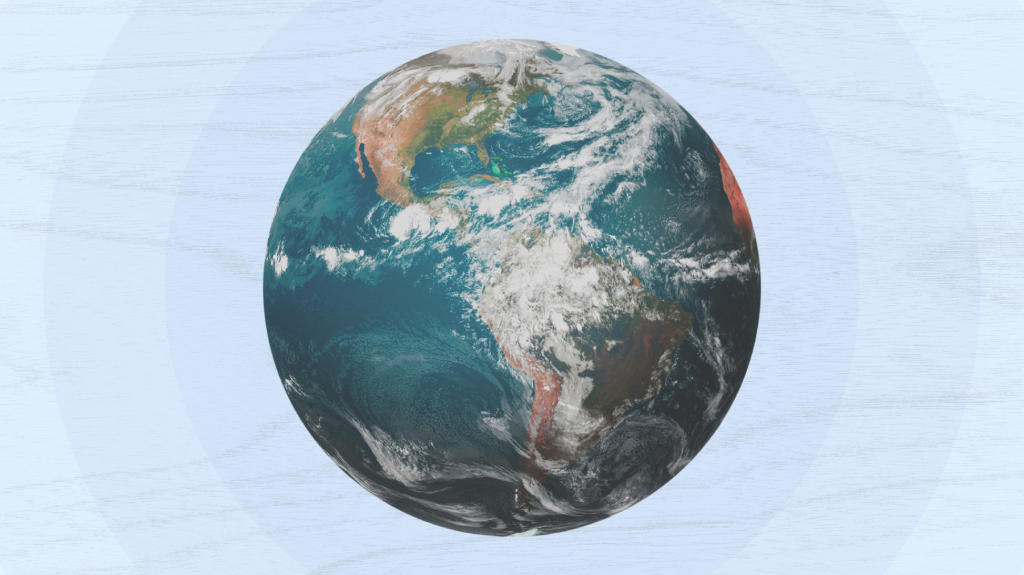
Sustainability in Construction
Sustainable construction practices can help improve profitability and win more business.
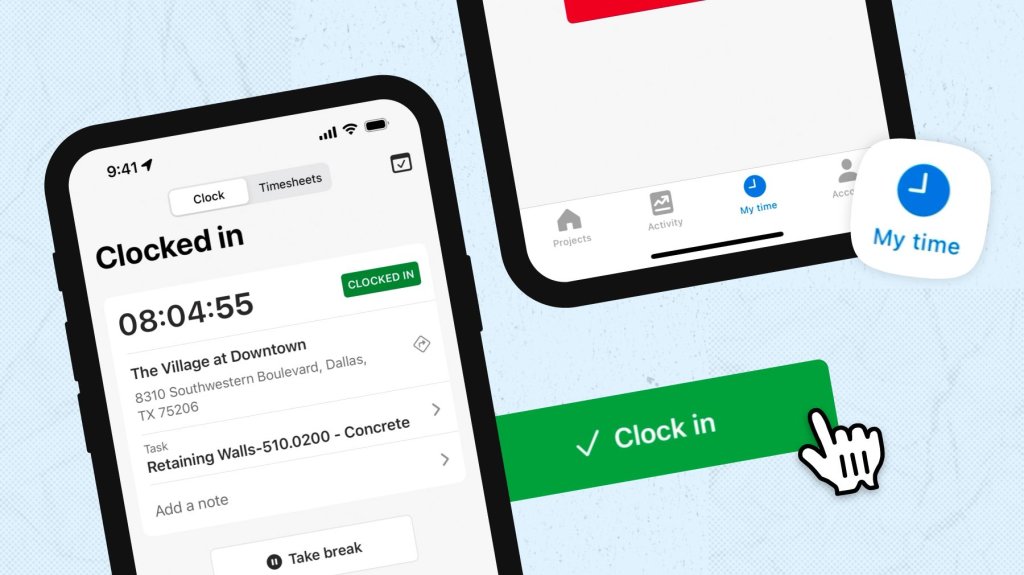
How to Clock in Crews
On Raken’s mobile app, you can easily manage employee time and clock in your crews in bulk right from the jobsite.
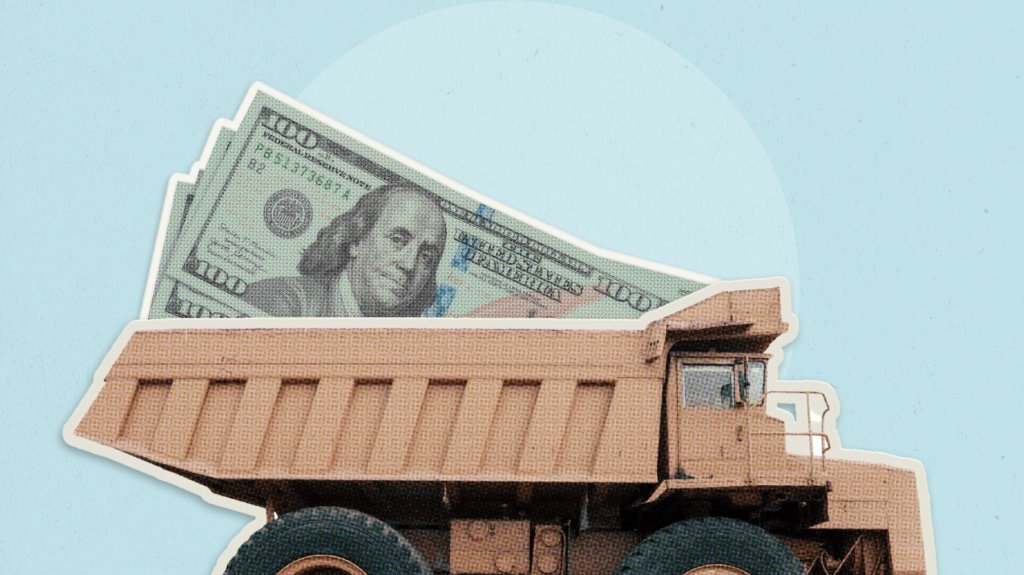
5 Ways to Cut Costs in Construction
Trying to increase ROI is a constant battle. Get tips for effectively reducing unnecessary costs and improving profitability.

How to Create a Heat Injury + Illness Prevention Plan
Learn how to proactively create a heat illness + injury prevention plan for your construction company (and how Raken can help).
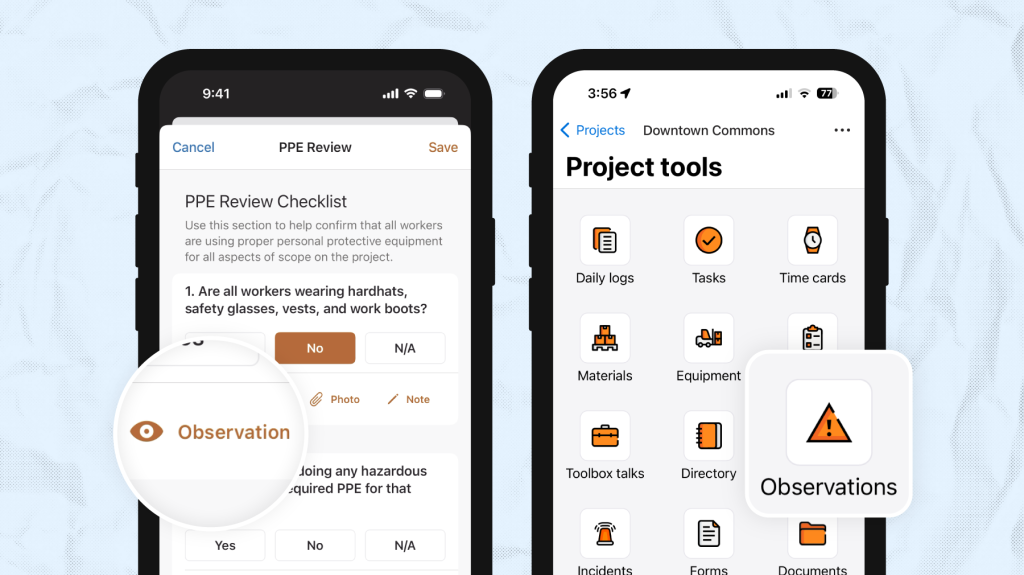
How to Submit Observations
See how Raken makes it easy to capture detailed safety and quality observations from the field.
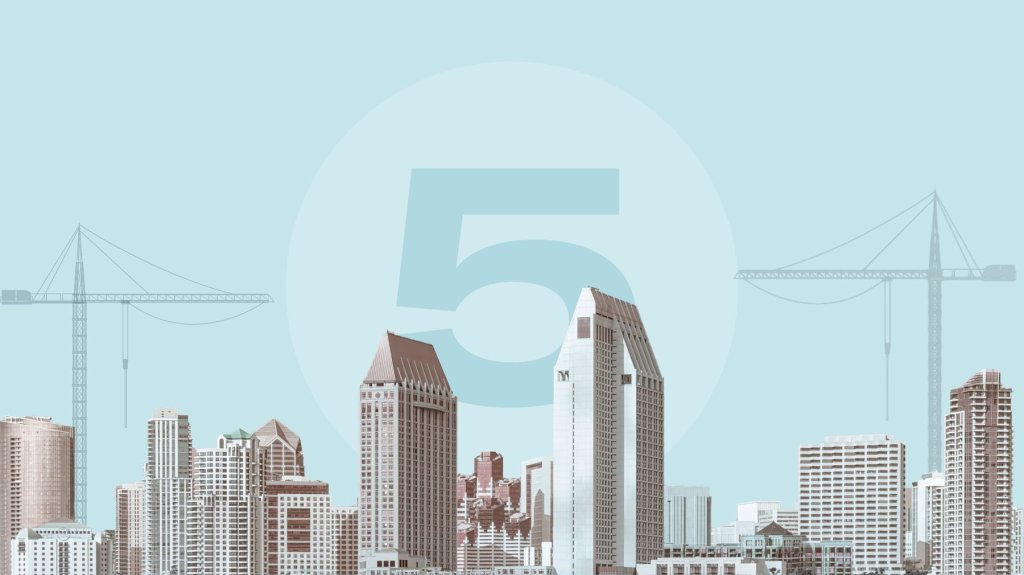
Made in the USA: Five Iconic Construction Projects in American History
We’ve highlighted a few of the most important milestones of American construction history.
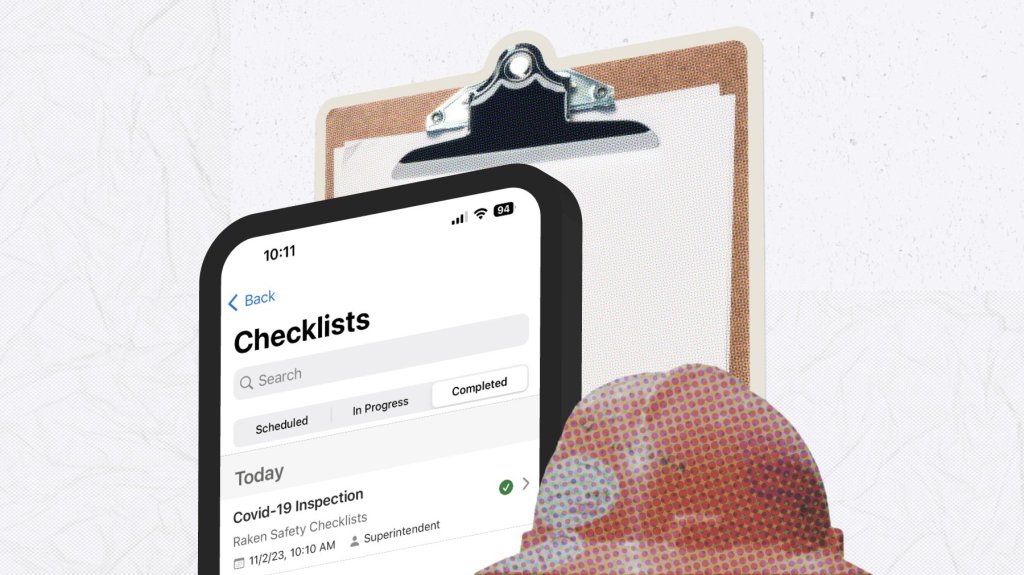
How to Improve (and Digitize) Your Construction Safety Checklists
Maximize the benefits of your safety and quality checklists with these best practices.
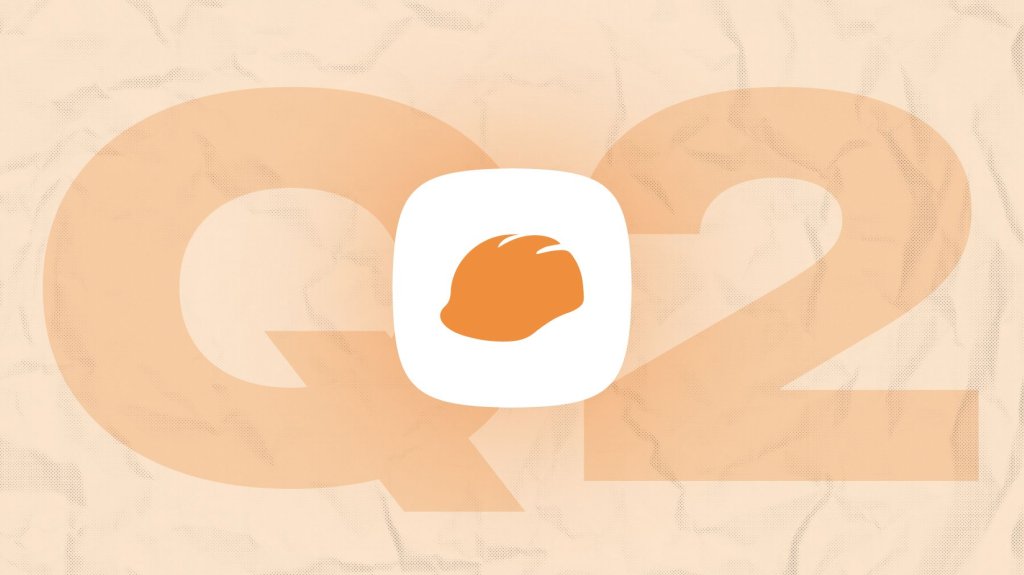
Quarterly Update: We’ve Been Busy
While you were breaking ground on new projects or finalizing existing ones, we were hard at work adding new features and improving efficiency.
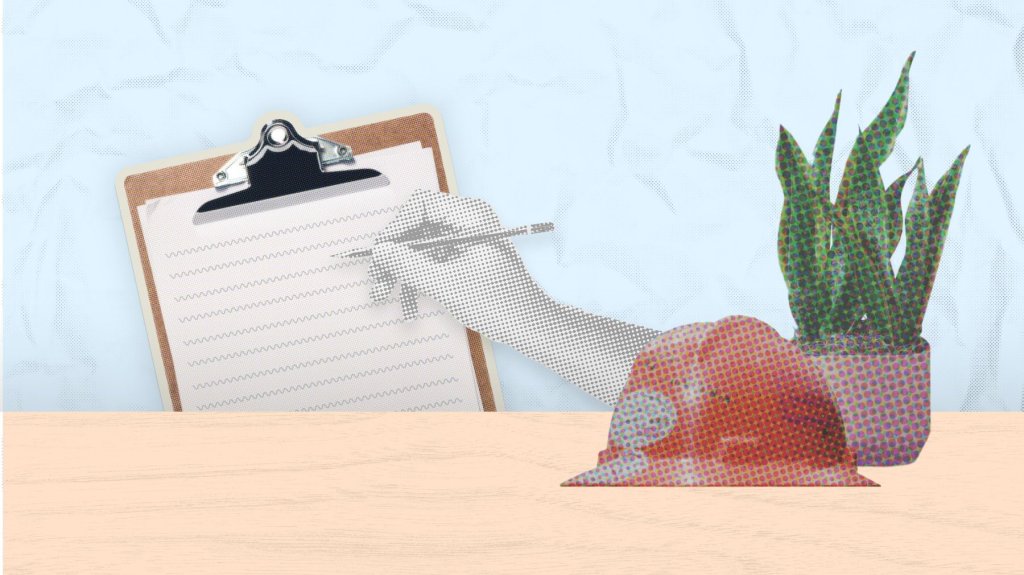
5 Construction Blog Ideas for General Contractors
Get simple tips for creating a professional blog for your general contracting business.