Blog
Catch up on all the latest construction tips, news, and updates.
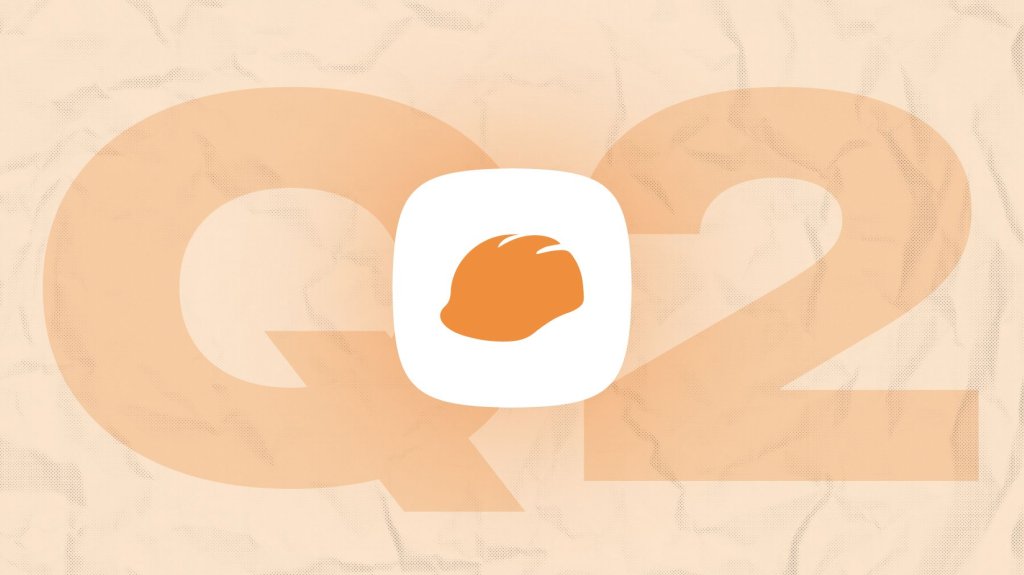
Quarterly Update: We’ve Been Busy
While you were breaking ground on new projects or finalizing existing ones, we were hard at work adding new features and improving efficiency.
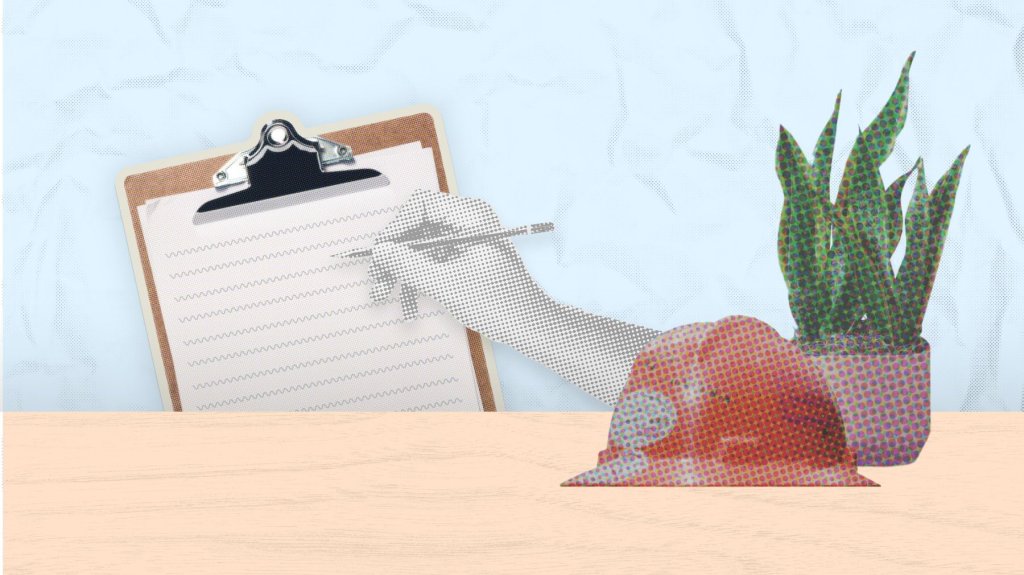
5 Construction Blog Ideas for General Contractors
Get simple tips for creating a professional blog for your general contracting business.
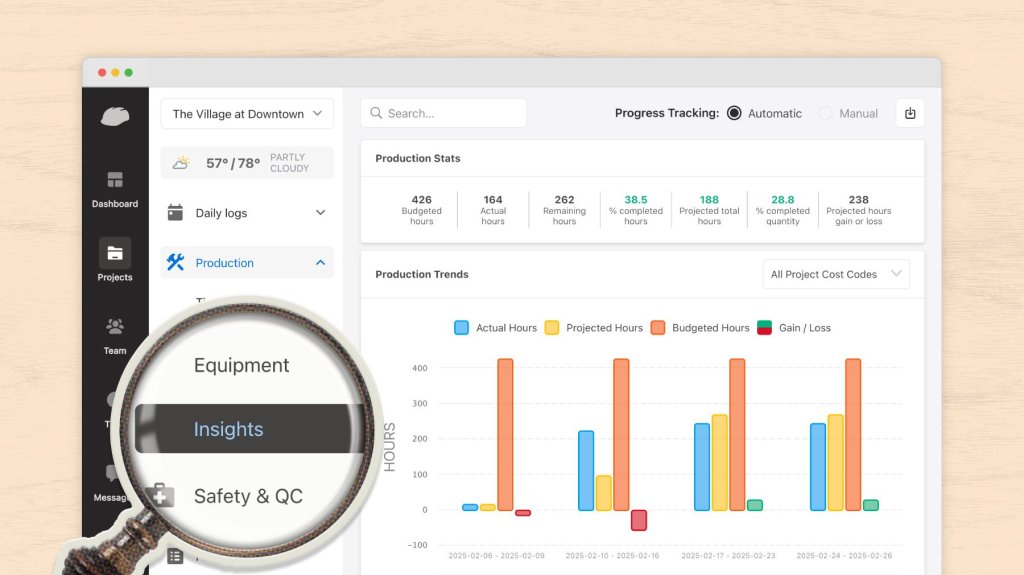
Business Intelligence Strategies for Construction Companies
It’s easy to get overwhelmed with data, but with modern tools, using business intelligence effectively as a construction company may be easier than you think.
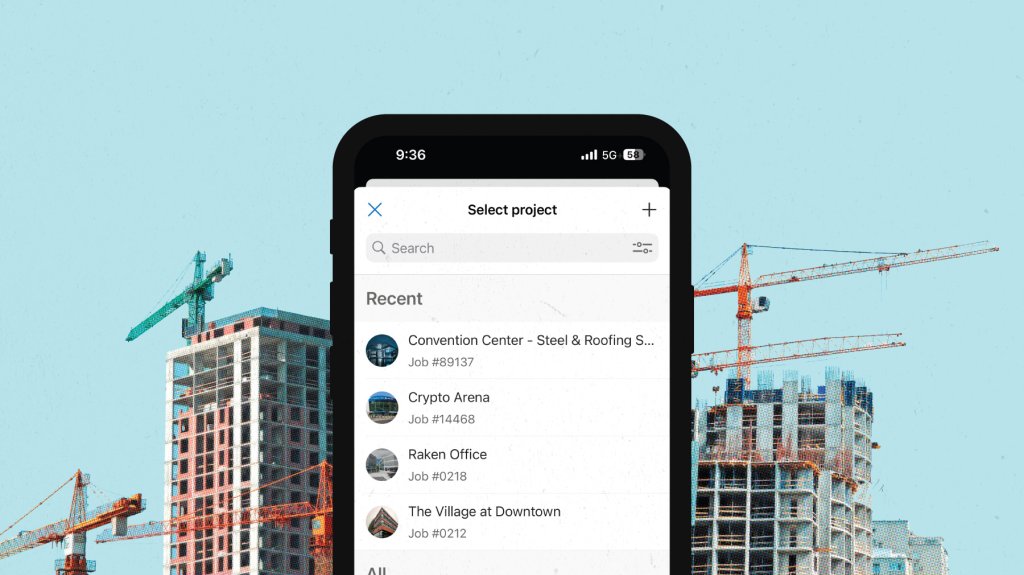
How to Write a Construction Case Study
Learn how to write an effective construction case study to help win more business.
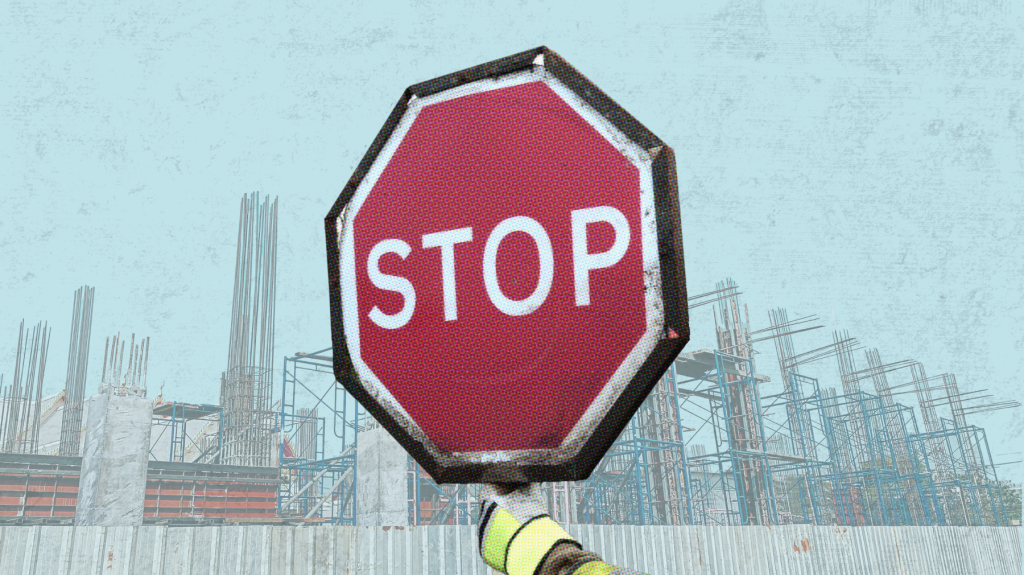
3 Ways to Prevent Abandoned Projects
Learn how to reduce the risk of your projects being abandoned and protect your business from lost profits.
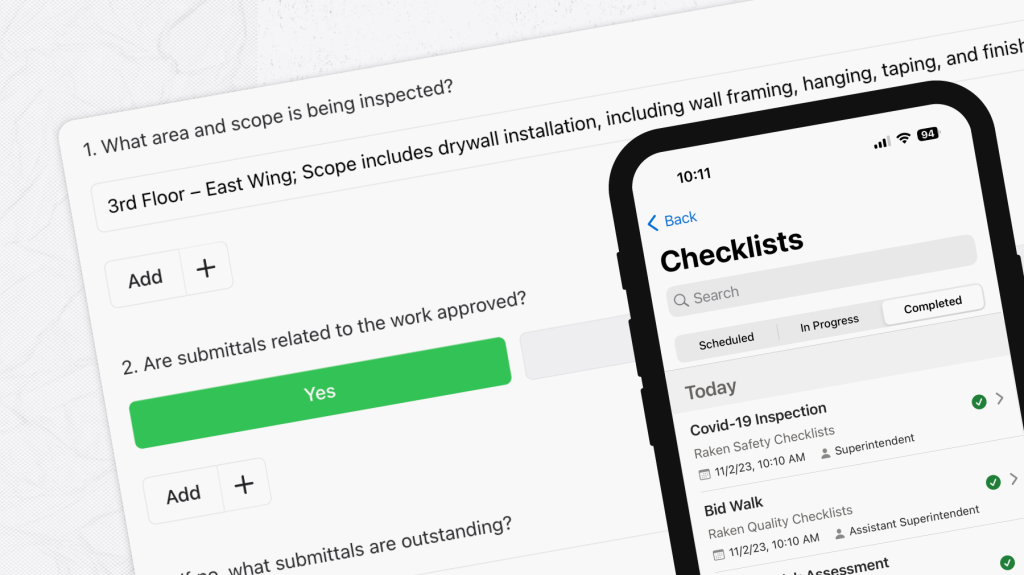
How to Create Custom Checklists
Learn how to create and assign your own custom checklists in Raken.
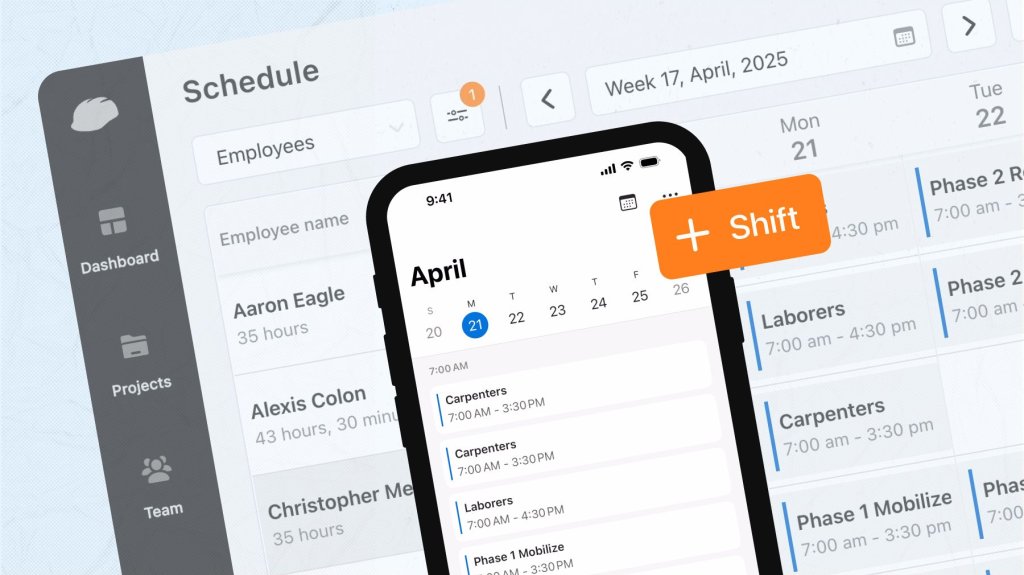
New Feature: Real-time Resource Scheduling
Get a calendar view of workers’ availability and more easily manage labor with Raken’s new resource scheduling tools.
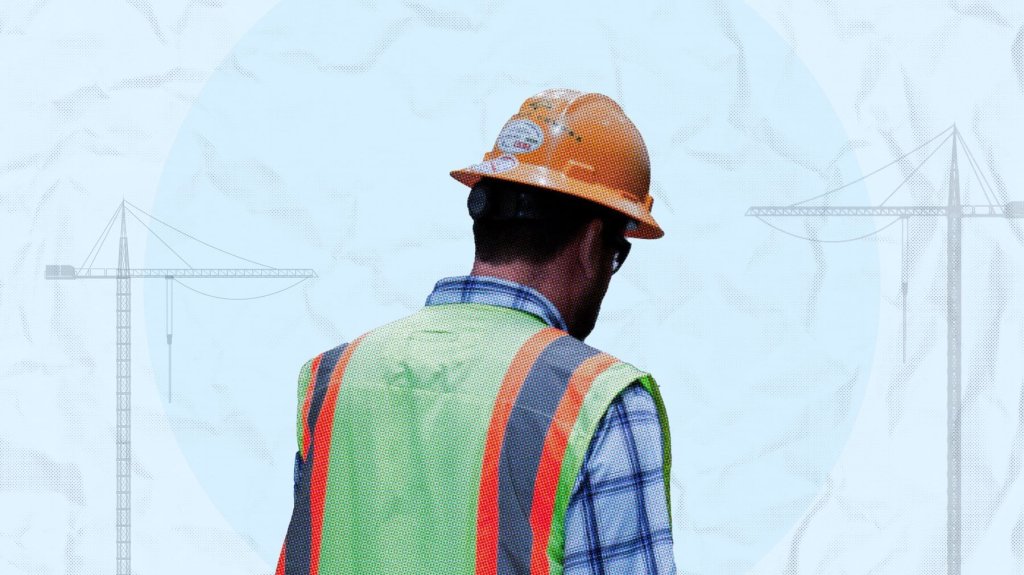
Resources for Mental Health in Construction
Learn how to recognize common mental health issues and get workers the help they need.
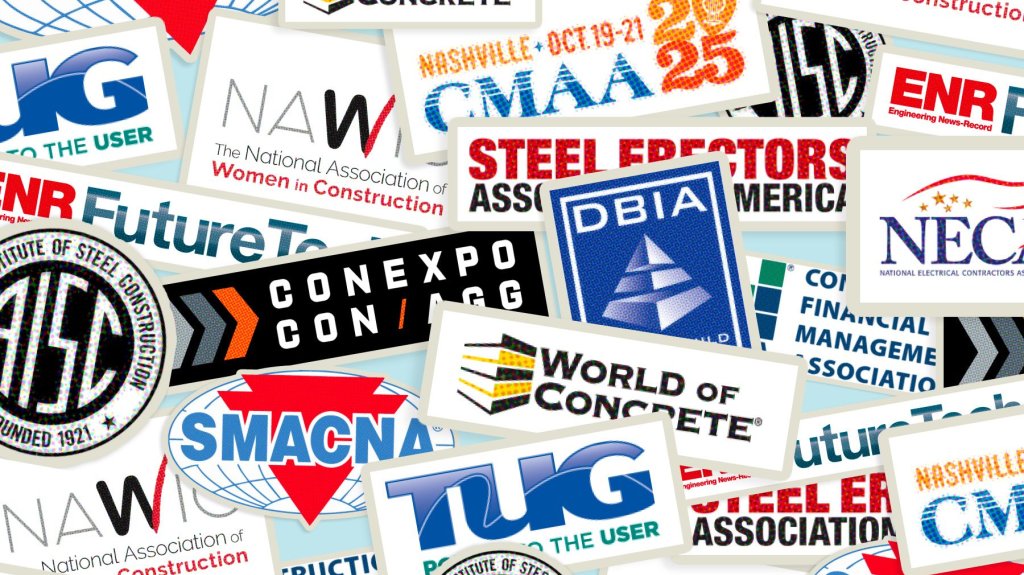
Top Construction Conferences, Trade Shows & Expos
Check out our list of the top construction conferences, conventions, trade shows, and expos across the U.S.
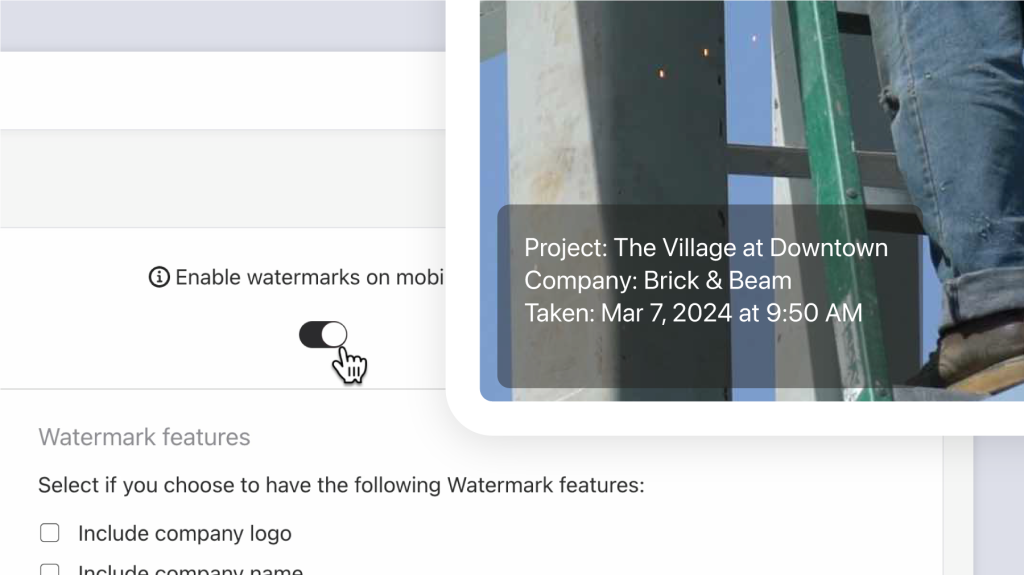
How to Enable Photo Watermarks
Learn how to add custom watermarks with your company logo, timestamps, and more to your jobsite photos in Raken’s easy-to-use field management app.
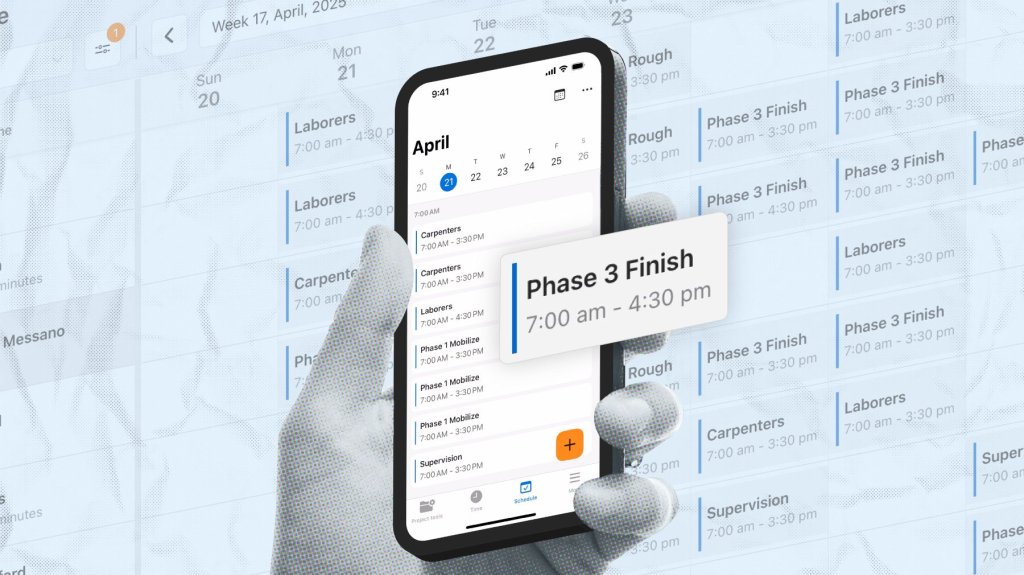
How to Better Manage Construction Crew Scheduling
Learn about the most common scheduling issues and how to manage them effectively.
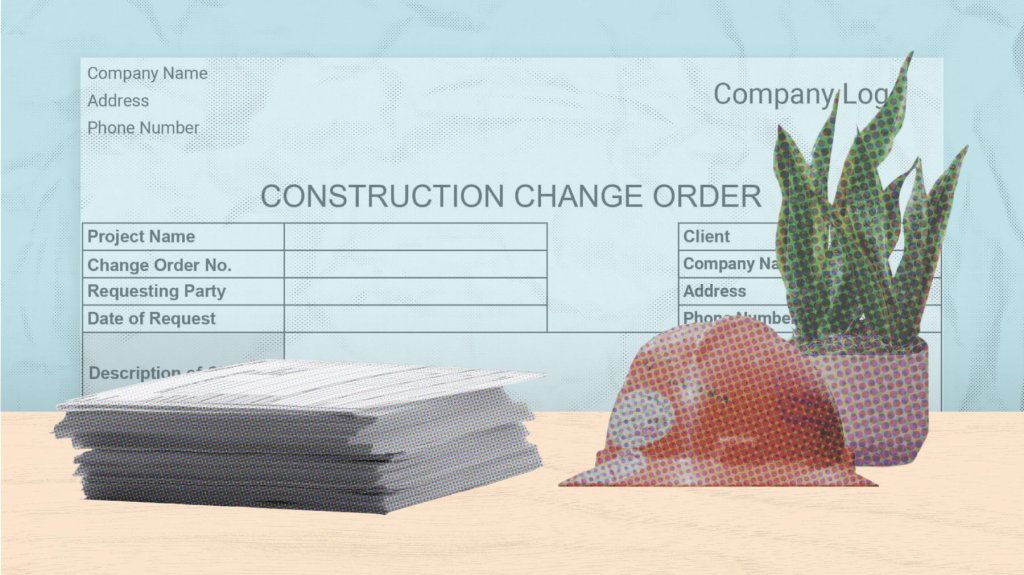
Why Do I Have Too Many Change Orders?
Learn some of the most common reasons you might have more change orders than usual on a project.